Flexible Manufacturing System Fms Definition And How It Works
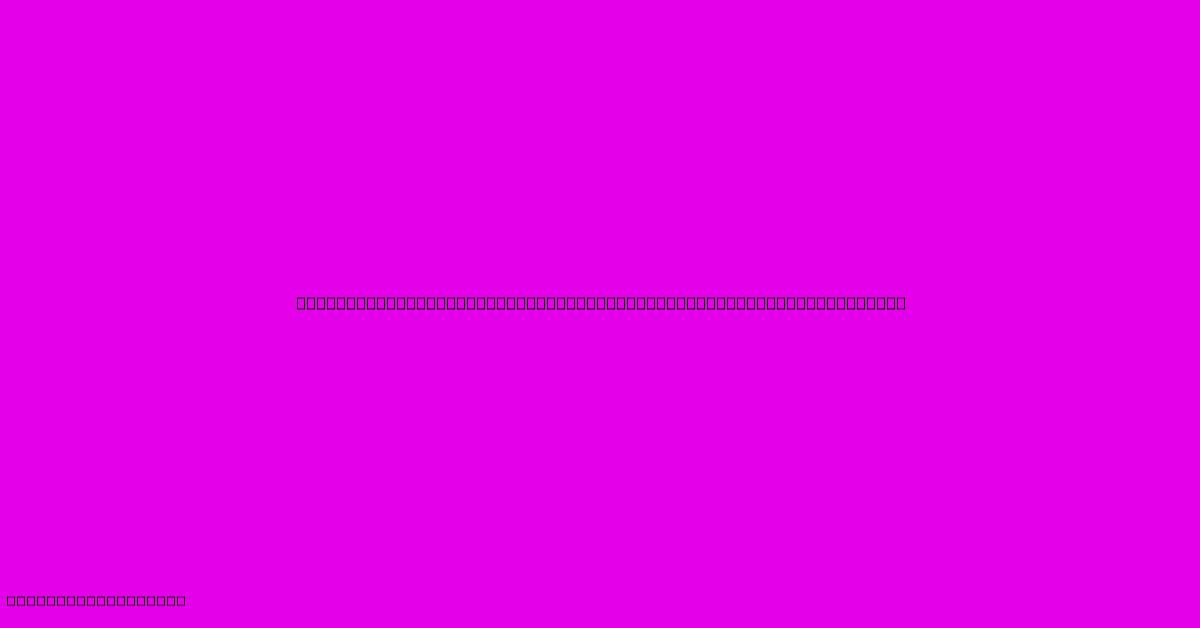
Discover more in-depth information on our site. Click the link below to dive deeper: Visit the Best Website meltwatermedia.ca. Make sure you don’t miss it!
Table of Contents
Unveiling the Power of Flexible Manufacturing Systems (FMS): A Comprehensive Guide
Hook: Does your manufacturing process feel rigid and inflexible, struggling to adapt to changing market demands? A bold statement: Implementing a Flexible Manufacturing System (FMS) can revolutionize your production efficiency and responsiveness.
Editor's Note: Nota del Editor: This comprehensive guide to Flexible Manufacturing Systems (FMS) was published today.
Relevance & Summary: In today's dynamic marketplace, adaptability is paramount. This article explores Flexible Manufacturing Systems (FMS), detailing their definition, operational mechanics, key components, advantages, and challenges. Understanding FMS principles is crucial for manufacturers seeking to enhance productivity, reduce costs, improve product quality, and quickly respond to shifting customer needs. Keywords include: flexible manufacturing systems, FMS, automation, manufacturing processes, lean manufacturing, agile manufacturing, robotics, CNC machines, programmable logic controllers (PLCs), material handling systems, production scheduling, computer-integrated manufacturing (CIM).
Analysis: This guide synthesizes information from academic research, industry publications, and case studies to provide a clear, practical understanding of FMS implementation and management.
Key Takeaways:
- FMS enhances manufacturing flexibility and responsiveness.
- Key components include automated machines, material handling, and sophisticated control systems.
- Successful implementation requires careful planning and integration.
- Significant benefits include reduced production costs and lead times.
- Challenges include high initial investment and complex system integration.
Flexible Manufacturing Systems (FMS): A Deep Dive
Subheading: Flexible Manufacturing Systems (FMS)
Introduction: A Flexible Manufacturing System (FMS) represents a sophisticated approach to manufacturing, characterized by its ability to efficiently produce a variety of products with minimal changeover time. Unlike traditional mass production lines, FMS integrates automated machines, computerized control systems, and advanced material handling to create a highly adaptable and responsive production environment. This adaptability is crucial in responding to fluctuating market demands and minimizing production bottlenecks.
Key Aspects: The core elements of an FMS include:
- Automated Machines: Numerically Controlled (NC) and Computer Numerically Controlled (CNC) machines form the backbone, performing various operations with high precision and repeatability.
- Automated Material Handling Systems: Automated Guided Vehicles (AGVs), conveyor belts, and robots ensure the seamless movement of work-in-progress between machines.
- Centralized Control System: A sophisticated computer system manages and monitors the entire FMS, optimizing production scheduling, resource allocation, and overall system performance. This often involves Programmable Logic Controllers (PLCs) and sophisticated software.
- Computer-Integrated Manufacturing (CIM): FMS is a key component of CIM, integrating all aspects of manufacturing, from design to production planning and execution, into a unified system.
Discussion: Each aspect is intricately linked, fostering a dynamic interplay that enhances efficiency. For example, the centralized control system analyzes real-time data from individual machines and material handling systems to optimize production flow, minimizing idle time and maximizing throughput. The use of robotics adds another layer of flexibility, allowing for the handling of complex parts and the adaptation to different product configurations. Furthermore, the integration with enterprise resource planning (ERP) systems provides a holistic view of the manufacturing process, enhancing decision-making capabilities. The relationship between FMS and Lean/Agile manufacturing principles is symbiotic, as FMS facilitates the reduction of waste, inventory, and lead times, core tenets of these methodologies.
Understanding Key Components of FMS
Subheading: Automated Machines
Introduction: The heart of any FMS lies in its automated machines, primarily CNC machines. Their programmability allows them to switch between different manufacturing operations with minimal setup time.
Facets:
- Role: To perform various machining operations (milling, drilling, turning, etc.) with high precision and accuracy.
- Examples: CNC milling machines, CNC lathes, CNC routers.
- Risks & Mitigations: Machine malfunctions require robust maintenance programs and backup systems. Regular calibration ensures accuracy.
- Impacts & Implications: High precision, repeatable operations, reduced human error.
Subheading: Automated Material Handling Systems
Introduction: Efficient material flow is vital in an FMS. Automated material handling systems ensure work-in-progress moves smoothly between machines.
Facets:
- Role: To transport materials between machines and storage areas without manual intervention.
- Examples: AGVs, conveyor belts, robotic arms.
- Risks & Mitigations: System failures can disrupt the entire production flow; redundancy and robust maintenance are key.
- Impacts & Implications: Reduced lead times, improved throughput, minimized material handling costs.
Subheading: Centralized Control System
Introduction: The control system acts as the brain of the FMS, orchestrating all activities and ensuring optimal performance.
Facets:
- Role: To manage machine operations, material flow, and overall production scheduling.
- Examples: PLCs, supervisory control and data acquisition (SCADA) systems, manufacturing execution systems (MES).
- Risks & Mitigations: System failures require robust backup systems and disaster recovery plans. Regular software updates and security measures are critical.
- Impacts & Implications: Optimized production, real-time monitoring, improved decision-making.
The Synergy Between FMS and Lean Manufacturing Principles
Introduction: The connection between FMS and lean manufacturing principles is profound. FMS facilitates the implementation of lean manufacturing goals by minimizing waste and improving efficiency.
Further Analysis: FMS directly supports lean principles such as Just-in-Time (JIT) manufacturing by reducing inventory and lead times. The ability to quickly switch between different products minimizes the need for large buffer stocks. Furthermore, the centralized control system optimizes resource utilization, reducing waste associated with idle time or inefficient processes. This synergy results in improved overall equipment effectiveness (OEE) and reduced production costs.
Closing: Implementing FMS principles within a lean manufacturing framework is a powerful combination, enhancing productivity, responsiveness, and overall competitiveness. However, careful planning and system integration are crucial to realize the full potential of this synergistic approach.
FAQ: Flexible Manufacturing Systems
Introduction: This section addresses common questions about FMS.
Questions:
- Q: What are the primary benefits of implementing an FMS? A: Enhanced flexibility, reduced lead times, lower production costs, improved quality, and increased responsiveness to market demands.
- Q: What are the major challenges associated with FMS implementation? A: High initial investment costs, complex system integration, the need for skilled personnel, and potential integration issues with existing systems.
- Q: Is FMS suitable for all types of manufacturing? A: No, FMS is best suited for medium to high-volume production of a variety of products where flexibility and adaptability are key.
- Q: How does FMS differ from traditional manufacturing lines? A: FMS offers significantly greater flexibility and adaptability compared to traditional lines, which are often designed for high-volume production of a single product.
- Q: What role does software play in an FMS? A: Software is crucial for managing and controlling the entire system, including production scheduling, machine operation, and material handling.
- Q: What are the key performance indicators (KPIs) used to measure the effectiveness of an FMS? A: OEE, throughput, lead time, inventory levels, and production costs.
Summary: Understanding the capabilities and limitations of FMS is vital for effective implementation.
Tips for Successful FMS Implementation
Introduction: These tips aid successful implementation and optimization of FMS.
Tips:
- Thorough Planning: Conduct a detailed feasibility study before implementation.
- Modular Design: Adopt a modular design approach to enable easier expansion and adaptation.
- Skilled Workforce: Invest in training and development for personnel.
- Robust Maintenance Program: Establish a comprehensive preventive and corrective maintenance program.
- Continuous Improvement: Implement a continuous improvement methodology such as Kaizen to continually optimize system performance.
- Integration with ERP Systems: Ensure seamless integration with existing ERP systems.
- Data Analytics: Utilize data analytics to identify areas for improvement and optimize production parameters.
Summary: These tips are vital for maximizing the benefits of an FMS.
Summary: Flexible Manufacturing Systems
Summary: This article comprehensively explored Flexible Manufacturing Systems (FMS), defining their core components, operational mechanics, and significant benefits. The synergy between FMS and lean manufacturing principles was highlighted, emphasizing the advantages of integrating these concepts for improved efficiency and competitiveness. Challenges associated with implementation were also addressed, providing a realistic assessment of the complexities involved.
Closing Message: Mensaje Final: The adoption of FMS signifies a significant step toward creating agile and responsive manufacturing environments. By embracing advanced technologies and strategic planning, manufacturers can unlock the transformative potential of FMS, establishing a sustainable competitive advantage in today's rapidly evolving global marketplace. The future of manufacturing undoubtedly rests on the ability to adapt and innovate, and FMS offers a powerful pathway toward that future.
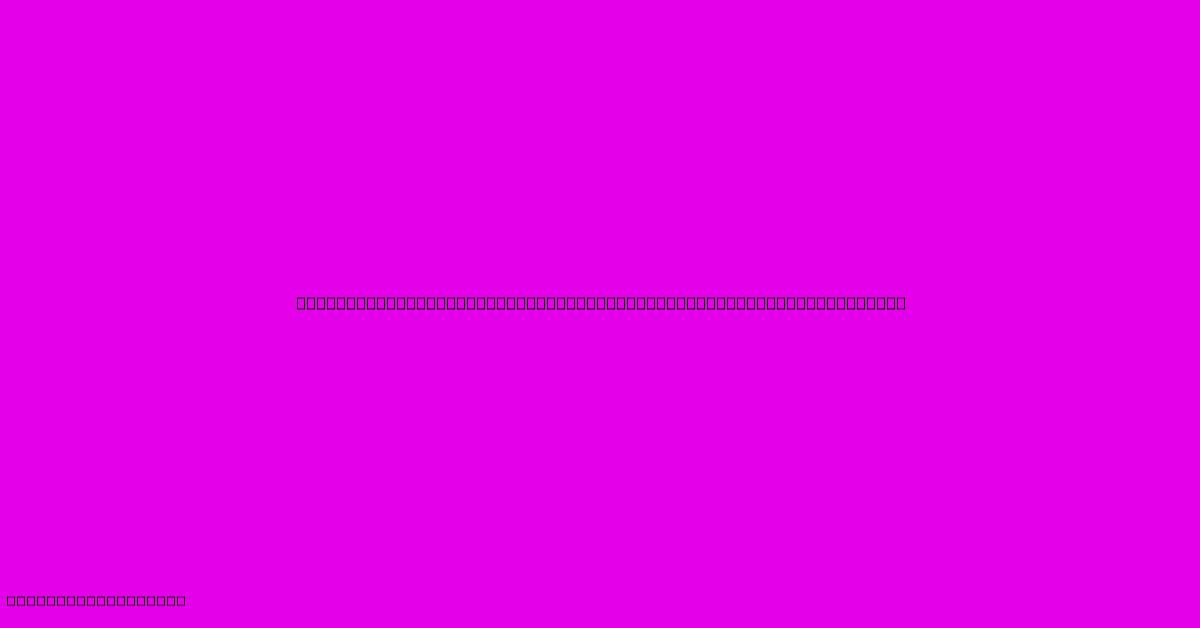
Thank you for taking the time to explore our website Flexible Manufacturing System Fms Definition And How It Works. We hope you find the information useful. Feel free to contact us for any questions, and don’t forget to bookmark us for future visits!
We truly appreciate your visit to explore more about Flexible Manufacturing System Fms Definition And How It Works. Let us know if you need further assistance. Be sure to bookmark this site and visit us again soon!
Featured Posts
-
Federal Employee Retirement System Fers Definition
Jan 07, 2025
-
How Much Is Fluoxetine Without Insurance
Jan 07, 2025
-
How To Shop On Amazon For Small Businesses
Jan 07, 2025
-
Energy Risk Professional Erp Definition
Jan 07, 2025
-
Equity Linked Note Eln Definition And Features
Jan 07, 2025