Occupational Safety And Health Act Definition And Requirements
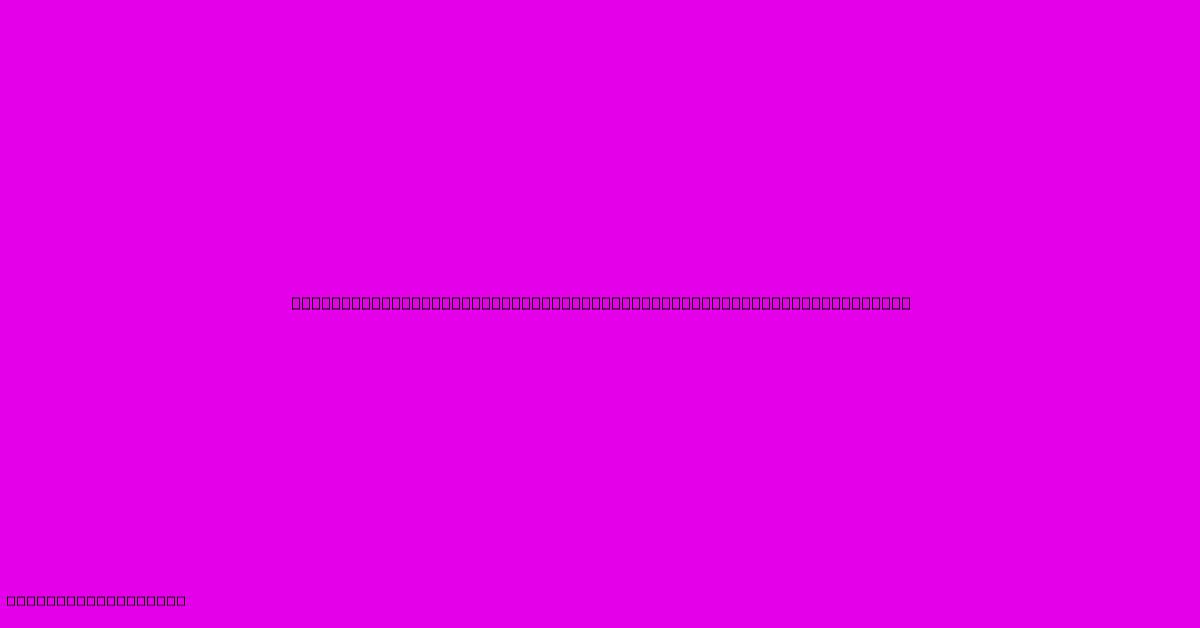
Discover more in-depth information on our site. Click the link below to dive deeper: Visit the Best Website meltwatermedia.ca. Make sure you don’t miss it!
Table of Contents
Unveiling Occupational Safety and Health Act: Definitions, Requirements & Compliance
Hook: Does your workplace prioritize employee well-being? A robust understanding of Occupational Safety and Health Acts (OSHAs) is crucial for fostering a safe and productive environment. Failure to comply can lead to devastating consequences.
Editor's Note: This comprehensive guide to Occupational Safety and Health Act definitions and requirements was published today.
Relevance & Summary: This article delves into the critical aspects of Occupational Safety and Health Acts, examining their core definitions, outlining key requirements for employers, and highlighting the importance of proactive compliance. Understanding OSHA regulations is vital for minimizing workplace hazards, preventing injuries and illnesses, and ensuring a healthy and productive workforce. This guide covers topics such as hazard identification, risk assessment, safety training, and record-keeping, providing a foundational understanding for employers and employees alike. Semantic keywords include workplace safety, hazard prevention, risk management, safety regulations, employee protection, and legal compliance.
Analysis: This guide synthesizes information from various authoritative sources, including legal texts, industry best practices, and safety standards organizations, to present a clear and concise overview of OSHA requirements. The analysis focuses on providing practical insights and actionable steps for organizations seeking to establish and maintain robust occupational safety and health programs.
Key Takeaways:
- OSHA defines workplace safety standards.
- Employers have legal obligations to provide safe workplaces.
- Employee training and participation are essential.
- Regular inspections and hazard assessments are mandatory.
- Record-keeping and reporting are crucial for compliance.
Transition: The following sections provide a detailed exploration of the key components of Occupational Safety and Health Acts, emphasizing their importance and practical application.
Occupational Safety and Health Act: A Deep Dive
Introduction
Occupational Safety and Health Acts (OSHAs), while varying slightly by jurisdiction, fundamentally aim to ensure safe and healthy working conditions for all employees. These acts establish a framework of legal obligations for employers and rights for workers, covering a wide range of potential hazards across diverse industries. The core principle is the prevention of workplace injuries, illnesses, and fatalities through proactive hazard management and risk mitigation strategies. This involves a multifaceted approach encompassing hazard identification, risk assessment, control measures, employee training, and ongoing monitoring.
Key Aspects of OSHA
The key aspects of any OSHA encompass:
- Hazard Identification and Risk Assessment: This is the foundational step. Employers must systematically identify potential hazards within their workplaces, evaluating the associated risks and their potential severity. This involves considering various factors, such as the nature of the hazard, the likelihood of exposure, and the potential consequences of exposure.
- Safety Training and Education: Comprehensive safety training is mandatory for all employees. Training programs must be tailored to specific job roles and hazards and must cover topics such as safe work practices, emergency procedures, hazard recognition, and the use of personal protective equipment (PPE).
- Personal Protective Equipment (PPE): Employers are required to provide and ensure the proper use of appropriate PPE. This might include safety glasses, hard hats, gloves, respirators, and other equipment designed to protect employees from specific hazards. Training on the correct selection, use, and maintenance of PPE is also critical.
- Emergency Preparedness and Response: Every workplace needs a well-defined emergency plan, including procedures for handling various scenarios, such as fires, chemical spills, and medical emergencies. Employees should receive training on emergency procedures and evacuation plans.
- Record-Keeping and Reporting: Maintaining accurate records of workplace injuries, illnesses, and near misses is essential for monitoring safety performance and identifying areas for improvement. Many OSHAs require employers to report certain types of incidents to regulatory authorities.
- Compliance Inspections and Audits: Regular workplace inspections and safety audits are necessary to identify existing and potential hazards, ensure compliance with regulations, and monitor the effectiveness of safety programs.
- Employee Participation and Consultation: Employee involvement is crucial for successful safety programs. OSHAs often include provisions for employee participation in hazard identification, risk assessment, and the development of safety procedures. This participation fosters a culture of safety and enhances the effectiveness of safety initiatives.
Hazard Identification and Risk Assessment
Introduction
This section delves into the crucial process of identifying and assessing workplace hazards, a cornerstone of any effective occupational safety and health program. The systematic identification of hazards, followed by a comprehensive risk assessment, provides a foundation for developing effective control measures and minimizing the potential for accidents and injuries.
Facets of Hazard Identification and Risk Assessment
- Roles: The responsibility for hazard identification and risk assessment often lies with the employer, supported by safety officers and other designated personnel. Employee involvement through safety committees is often encouraged.
- Examples: Identifying hazards might include recognizing unguarded machinery, identifying chemical spills, assessing ergonomic risks associated with repetitive tasks, or recognizing electrical hazards.
- Risks and Mitigations: Risks are evaluated based on the likelihood of exposure and the severity of potential harm. Mitigation strategies range from eliminating hazards altogether to using engineering controls, administrative controls, and PPE.
- Impacts and Implications: Failing to identify and adequately assess risks can lead to workplace accidents, injuries, illnesses, and legal repercussions for the employer.
Summary
Effective hazard identification and risk assessment are proactive measures that significantly reduce workplace incidents. They form the basis for implementing appropriate control measures and preventing harm to employees. A comprehensive risk assessment ensures that the most significant hazards receive the highest priority in mitigation efforts.
Employee Training and Participation
Introduction
Employee training and active participation are vital for successful occupational safety and health management. A safe working environment is not just the responsibility of management; it requires the collective efforts of all employees. This section explores the importance of comprehensive training and engagement strategies.
Further Analysis
Effective training programs must be tailored to the specific needs of each job role, covering relevant hazards, safe work practices, and emergency procedures. Regular refresher training is essential to maintain employee competence and address changes in procedures or technologies. Interactive training methods, such as practical demonstrations and hands-on exercises, enhance understanding and retention. Employee participation in safety committees or regular safety meetings provides a platform for sharing concerns, discussing safety issues, and proactively identifying potential hazards. A strong culture of safety, fostered by open communication and mutual respect, is critical to success.
Closing
Investing in comprehensive employee training and promoting active participation are integral components of a robust occupational safety and health program. This creates a safer work environment, reduces the risk of incidents, and promotes a positive safety culture.
FAQ: Occupational Safety and Health Act
Introduction
This section answers frequently asked questions about Occupational Safety and Health Acts.
Questions
- Q: What are the penalties for non-compliance with OSHA regulations? A: Penalties can vary significantly depending on the severity of the violation and the jurisdiction but can include fines, legal action, and reputational damage.
- Q: Who is responsible for enforcing OSHA regulations? A: This is usually a government agency, often an OSHA or equivalent body.
- Q: Do small businesses have different requirements under OSHA? A: While the core principles remain the same, there might be some flexibility or tailored guidance for smaller businesses, particularly regarding record-keeping or the complexity of safety programs.
- Q: What are the reporting requirements for workplace injuries? A: Reporting requirements vary by jurisdiction and severity of the injury. Serious injuries or fatalities usually require immediate reporting.
- Q: How often should workplace safety inspections be conducted? A: Regular inspections should be conducted, the frequency depending on the level of risk and the nature of the work. More hazardous workplaces would necessitate more frequent inspections.
- Q: Can employees refuse unsafe work? A: In many jurisdictions, employees have the right to refuse unsafe work if they genuinely believe it poses an imminent risk to their health or safety.
Summary
Understanding OSHA regulations and requirements is crucial for all workplaces. Compliance is not merely a legal obligation; it’s a commitment to employee well-being and a foundation for a productive and safe working environment.
Transition: This leads us to practical tips for effective OSHA compliance.
Tips for Effective OSHA Compliance
Introduction
This section outlines practical tips to assist organizations in achieving and maintaining robust OSHA compliance.
Tips
- Develop a comprehensive written safety program: This program should outline procedures for hazard identification, risk assessment, training, emergency response, and record-keeping.
- Conduct regular safety inspections: Systematic inspections are essential to identify and address potential hazards promptly.
- Provide thorough safety training: Training must be specific to job roles and cover relevant hazards and safety procedures.
- Implement effective engineering controls: Where feasible, engineering controls should be prioritized to eliminate or reduce hazards at their source.
- Use personal protective equipment (PPE) appropriately: Provide appropriate PPE and ensure employees understand its proper use and maintenance.
- Promote a strong safety culture: Foster a culture of safety where employees feel empowered to report hazards and participate in safety initiatives.
- Maintain accurate records: Keep detailed records of safety training, inspections, incidents, and any corrective actions.
- Stay updated on OSHA regulations: Regulations can change, so staying informed is critical for maintaining compliance.
Summary
By implementing these tips, organizations can significantly enhance their OSHA compliance, creating a safer and more productive work environment for all.
Summary of Occupational Safety and Health Act Requirements
Summary: This article explored the key definitions and requirements of Occupational Safety and Health Acts, emphasizing the crucial role of hazard identification, risk assessment, employee training, and proactive compliance strategies.
Closing Message: Prioritizing occupational safety and health is not merely a legal obligation; it's an ethical imperative. By fostering a culture of safety and adhering to OSHA regulations, organizations can create a workplace where employees can thrive, contributing to a more productive and sustainable future. Investing in robust safety programs is an investment in the well-being of your workforce and the success of your organization.
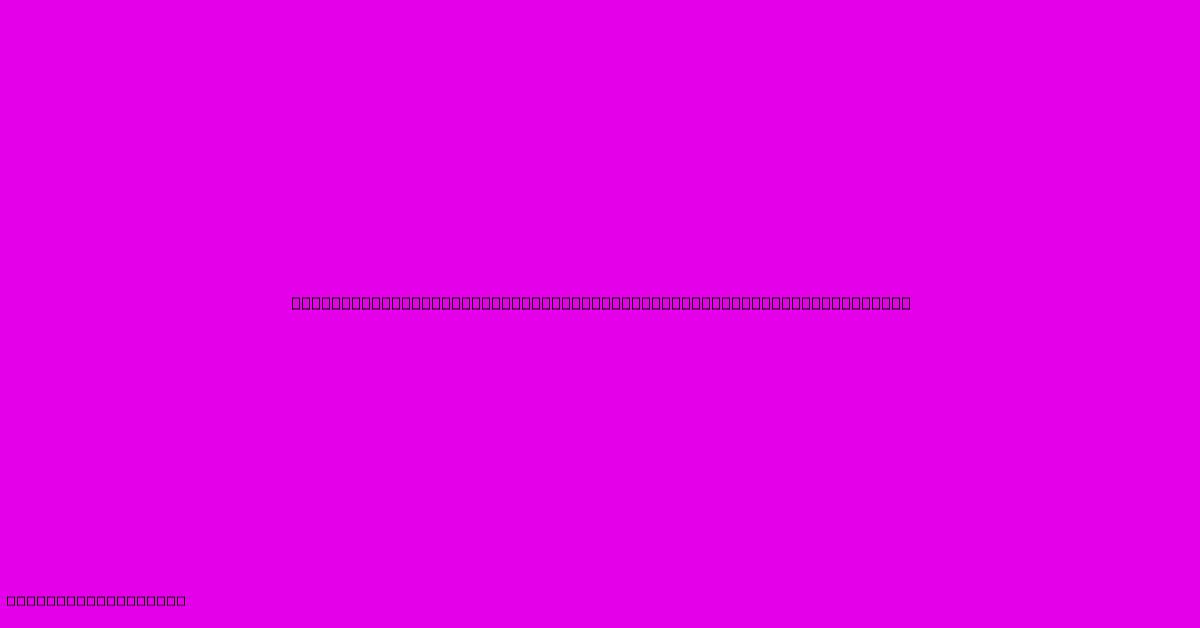
Thank you for taking the time to explore our website Occupational Safety And Health Act Definition And Requirements. We hope you find the information useful. Feel free to contact us for any questions, and don’t forget to bookmark us for future visits!
We truly appreciate your visit to explore more about Occupational Safety And Health Act Definition And Requirements. Let us know if you need further assistance. Be sure to bookmark this site and visit us again soon!
Featured Posts
-
Centers For Medicare Medicaid Services Cms Definition How It Works
Jan 03, 2025
-
Normalized Earnings Definition Purpose Benefits And Examples
Jan 03, 2025
-
Chastity Bond Definition
Jan 03, 2025
-
How Can I Lower My Private Student Loan Payments
Jan 03, 2025
-
How To Use Credit On Doordash
Jan 03, 2025