Original Equipment Manufacturer Oem Definition And Examples
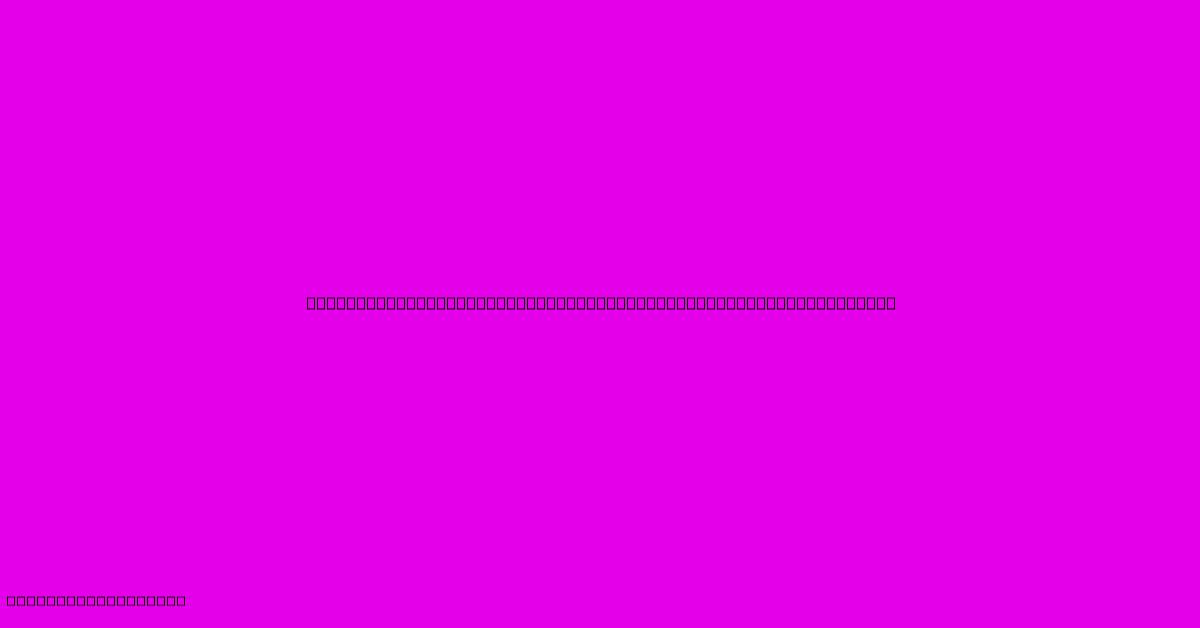
Discover more in-depth information on our site. Click the link below to dive deeper: Visit the Best Website meltwatermedia.ca. Make sure you don’t miss it!
Table of Contents
Unveiling the OEM: Definition, Examples & Industry Impact
Does your business understand the crucial role of Original Equipment Manufacturers (OEMs)? A clear grasp of OEMs is vital for navigating today's complex supply chains and leveraging strategic partnerships. This comprehensive guide explores the definition, examples, and significant impact of OEMs across various industries.
Editor's Note: This definitive guide to Original Equipment Manufacturers (OEMs) was published today.
Relevance & Summary: Understanding Original Equipment Manufacturers (OEMs) is critical for businesses involved in manufacturing, supply chain management, and product development. This article provides a detailed overview of OEMs, encompassing their definition, diverse examples across industries, and the significant role they play in global commerce. Keywords like original equipment manufacturer, supply chain, manufacturing, contract manufacturing, private label, white label, and branding will be used throughout to enhance SEO optimization.
Analysis: This article draws upon extensive research across reputable industry publications, case studies of successful OEM partnerships, and in-depth analysis of global supply chain dynamics. The information presented aims to deliver a clear, concise, and insightful understanding of the OEM landscape.
Key Takeaways:
- Clear definition of Original Equipment Manufacturers (OEMs)
- Diverse examples of OEMs across multiple sectors
- Advantages and disadvantages of OEM partnerships
- The evolving role of OEMs in global manufacturing
- Future trends impacting the OEM landscape
What is an Original Equipment Manufacturer (OEM)?
An Original Equipment Manufacturer (OEM) is a company that produces parts or finished goods which are then used by another company to produce their own branded products. OEMs often specialize in specific components or sub-assemblies, leveraging expertise and economies of scale to offer competitive pricing and high-quality manufacturing. This contrasts with companies that manufacture finished goods under their own brand name. The core characteristic of an OEM relationship lies in the supply of components or products to another company for integration into a larger final product, rather than direct-to-consumer sales of their manufactured goods.
Key Aspects of OEM Relationships
Understanding the nuances of OEM relationships requires examining several crucial aspects:
1. Contractual Agreements: OEM relationships are governed by formal contracts specifying the type and quantity of goods to be supplied, quality standards, delivery schedules, and intellectual property rights. These contracts are critical in ensuring both parties’ interests are protected and expectations are clearly defined.
2. Specialized Manufacturing: OEMs frequently specialize in particular components, processes, or manufacturing technologies. This specialization enables them to achieve efficiencies and provide high-quality output at competitive costs, leveraging advanced equipment and skilled labor.
3. Intellectual Property (IP): IP considerations are paramount. Contracts often stipulate which party owns the intellectual property associated with the components or products supplied. This aspect is crucial for protecting innovations and preventing disputes.
4. Quality Control: Rigorous quality control is essential. OEMs must adhere to strict quality standards set by the company integrating their components or products into a finished good. Regular inspections and adherence to international quality standards (like ISO 9001) are commonplace.
Examples of OEMs Across Industries
The role of OEMs is pervasive across a multitude of industries. Below are some examples showcasing the breadth of OEM involvement:
1. Automotive Industry: The automotive sector is a prime example of extensive OEM utilization. Companies like Bosch supply essential components such as engine management systems, brakes, and electronics to major car manufacturers. Other OEMs specialize in tires, seats, and other internal components.
2. Electronics Industry: In the electronics industry, countless OEMs provide vital components for smartphones, computers, and other devices. Companies manufacture chipsets, displays, batteries, and other essential parts that are then integrated by brands like Apple, Samsung, and Dell.
3. Aerospace Industry: The aerospace industry relies heavily on OEMs for the production of specialized parts and sub-assemblies for aircraft and spacecraft. OEMs might produce engine components, avionics systems, or structural elements that are integrated into larger aircraft or satellite systems.
4. Medical Device Industry: The medical device sector utilizes OEMs extensively for the production of components for medical instruments and equipment. Companies specialize in creating components such as sensors, actuators, and microfluidic devices that are then integrated into sophisticated medical devices.
5. Consumer Goods Industry: Even in the consumer goods sector, OEMs play a significant role. Companies manufacture parts for household appliances, furniture, and sporting goods, supplying these components to larger brands.
OEM vs. Private Label vs. White Label
It's crucial to differentiate between OEM, private label, and white label manufacturing:
-
OEM (Original Equipment Manufacturer): As defined above, an OEM manufactures components or products for another company to integrate into their final product. The OEM's branding is usually not visible on the finished product.
-
Private Label: Private label manufacturing involves a company designing and branding products manufactured by another company. While the other company produces the product, the branding and packaging are entirely controlled by the company selling the finished goods.
-
White Label: White label manufacturing is similar to private label, but the product is often less customized. The manufacturer provides a generic product that the retailer can rebrand and sell under its name.
Advantages and Disadvantages of OEM Partnerships
Advantages:
-
Reduced Costs: OEMs can leverage economies of scale and specialized expertise to offer lower manufacturing costs than if a company produced everything in-house.
-
Access to Expertise: OEMs bring specialized knowledge and technological capabilities, eliminating the need for significant internal investment in research and development.
-
Increased Efficiency: Outsourcing manufacturing to an OEM can free up internal resources to focus on core competencies like design, marketing, and sales.
-
Faster Time to Market: Collaborating with an OEM can significantly reduce product development time and lead time for bringing new products to the market.
Disadvantages:
-
Loss of Control: Relying on an external manufacturer for essential components can reduce control over quality, production schedules, and intellectual property.
-
Dependency: Building a strong dependency on a single OEM can create vulnerabilities if there are disruptions in the supply chain.
-
Communication Challenges: Effective communication and collaboration between a company and an OEM is essential. Poor communication can lead to delays, misunderstandings, and quality issues.
-
Intellectual Property Risks: Careful consideration of intellectual property rights in OEM contracts is crucial to protect confidential information and innovative designs.
The Future of OEMs
The OEM landscape is constantly evolving, influenced by several key trends:
-
Globalization and Supply Chain Diversification: Companies are increasingly diversifying their supply chains to mitigate risks associated with geopolitical instability and disruptions.
-
Technological Advancements: Advances in automation, robotics, and AI are transforming manufacturing processes and influencing OEM partnerships.
-
Sustainability Concerns: Growing emphasis on sustainability and environmental responsibility is shaping OEM selection criteria, with companies seeking partners with strong sustainability commitments.
FAQ
Q1: What is the difference between an OEM and a contract manufacturer?
A1: While both OEMs and contract manufacturers produce goods for other companies, OEMs often focus on specific components or sub-assemblies, while contract manufacturers typically produce finished goods according to the client's specifications.
Q2: How do I find a reliable OEM?
A2: Thoroughly researching potential OEMs, verifying their capabilities and certifications (like ISO 9001), checking references, and negotiating clear contractual agreements are essential steps.
Q3: What are the key considerations for negotiating an OEM contract?
A3: Key considerations include specifying quality standards, delivery schedules, payment terms, intellectual property rights, and dispute resolution mechanisms.
Q4: Can OEMs provide design services?
A4: Some OEMs offer design services, allowing companies to collaborate on product development from the initial concept to the final product.
Q5: What are the risks associated with outsourcing manufacturing to an OEM?
A5: Risks include supply chain disruptions, quality control issues, intellectual property breaches, and communication challenges.
Q6: How do I ensure quality control with an OEM?
A6: Regular inspections, clear quality standards in contracts, and establishing transparent communication channels are vital for ensuring product quality.
Tips for Successful OEM Partnerships
-
Thorough Due Diligence: Conduct comprehensive research to identify reputable and capable OEMs.
-
Clear Communication: Establish transparent and open communication channels to ensure seamless collaboration.
-
Detailed Contracts: Negotiate contracts that clearly define specifications, responsibilities, and intellectual property rights.
-
Regular Monitoring: Implement a system for regular monitoring of production processes and quality control.
-
Relationship Management: Nurture a strong long-term relationship with the chosen OEM to foster trust and mutual understanding.
-
Risk Mitigation: Develop strategies for mitigating risks associated with supply chain disruptions and other unforeseen challenges.
-
Continuous Improvement: Work collaboratively with the OEM to continually improve processes and product quality.
Summary
This comprehensive guide has explored the definition, examples, advantages, disadvantages, and future trends of Original Equipment Manufacturers (OEMs). Understanding this crucial aspect of global manufacturing is essential for businesses to navigate complex supply chains, optimize production, and leverage strategic partnerships effectively.
Closing Message
The strategic utilization of OEMs is no longer optional but a necessity for businesses aiming for growth and global competitiveness. By understanding the intricacies of OEM partnerships and implementing best practices, businesses can unlock significant cost efficiencies, gain access to specialized expertise, and accelerate their journey towards market leadership.
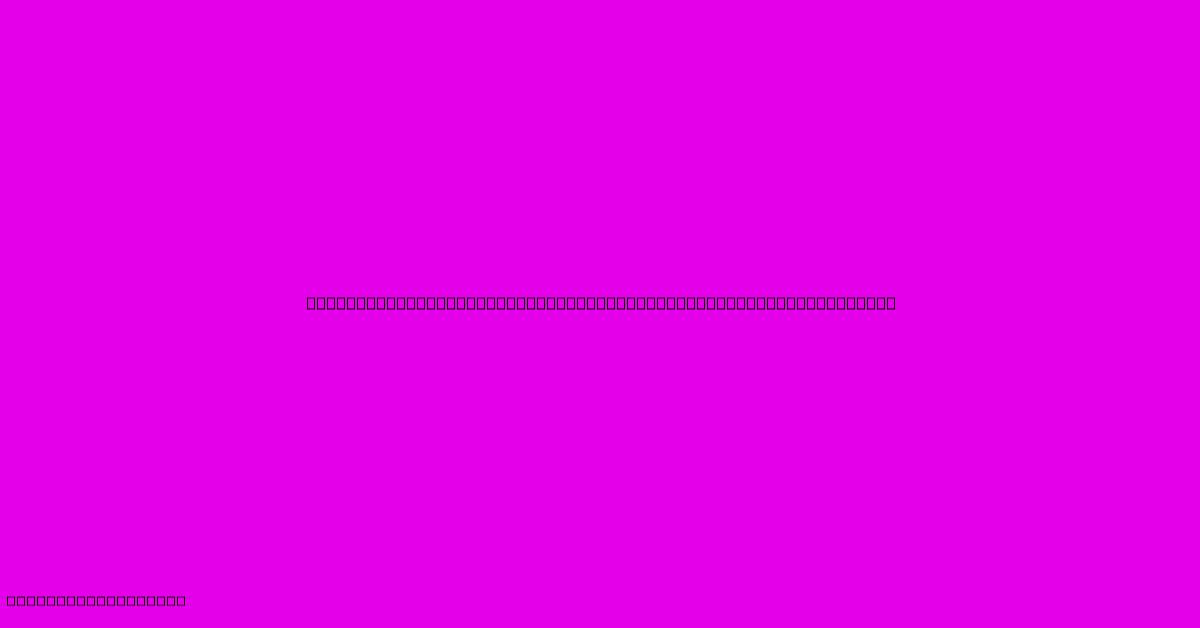
Thank you for taking the time to explore our website Original Equipment Manufacturer Oem Definition And Examples. We hope you find the information useful. Feel free to contact us for any questions, and don’t forget to bookmark us for future visits!
We truly appreciate your visit to explore more about Original Equipment Manufacturer Oem Definition And Examples. Let us know if you need further assistance. Be sure to bookmark this site and visit us again soon!
Featured Posts
-
Where Is Credit Union
Jan 03, 2025
-
Overcontribution Definition
Jan 03, 2025
-
What Is Credit Card Nickname
Jan 03, 2025
-
How Long Do I Have To Get Insurance On A New Car
Jan 03, 2025
-
What Is The Credit Limit On Amex Platinum
Jan 03, 2025