Pull Through Production Definition
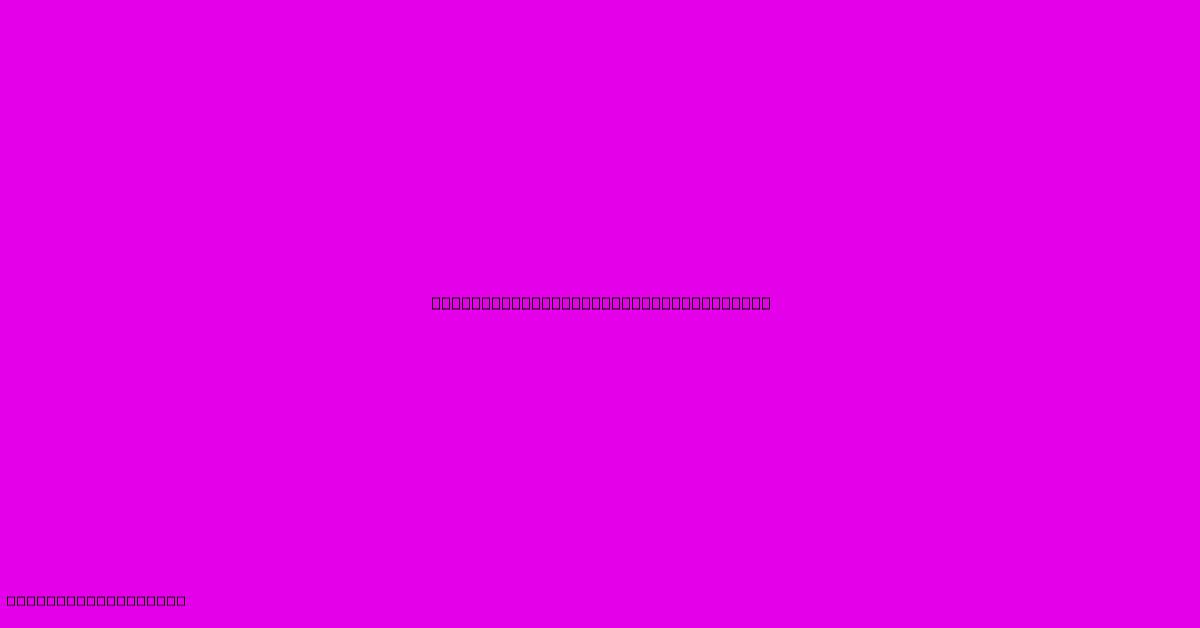
Discover more in-depth information on our site. Click the link below to dive deeper: Visit the Best Website meltwatermedia.ca. Make sure you don’t miss it!
Table of Contents
Unlocking Efficiency: A Deep Dive into Pull Through Production Definition
Hook: Does your manufacturing process struggle with inventory build-up and wasted resources? A robust pull through production system can revolutionize your efficiency.
Editor's Note: This comprehensive guide to pull through production has been published today.
Relevance & Summary: Understanding pull through production is crucial for any manufacturing or production environment aiming to optimize efficiency, minimize waste, and enhance responsiveness to market demand. This article provides a detailed explanation of pull through production, exploring its key aspects, benefits, and challenges. It will cover topics such as just-in-time inventory, lean manufacturing principles, and the role of technology in implementing a successful pull through system. Keywords include: pull through production, just-in-time (JIT), lean manufacturing, demand-pull system, inventory management, production planning, Kanban, value stream mapping.
Analysis: This guide is based on extensive research into lean manufacturing principles, just-in-time inventory systems, and current best practices in production management. It synthesizes information from academic journals, industry publications, and case studies of companies successfully implementing pull through production.
Key Takeaways:
- Pull through production prioritizes customer demand.
- It minimizes inventory waste and storage costs.
- It improves responsiveness to market fluctuations.
- It requires strong communication and collaboration.
- It relies on accurate demand forecasting.
Pull Through Production: A Definition and its Significance
Pull through production is a manufacturing strategy where production is triggered by actual customer demand, rather than relying on forecasts or predetermined production schedules. Unlike push systems, which produce goods based on anticipated demand and often lead to excess inventory, pull systems only produce what is needed, when it is needed. This "pull" mechanism is driven by real-time customer orders or signals indicating demand. This results in a leaner, more efficient, and responsive production process.
Key Aspects of Pull Through Production
Several key aspects characterize effective pull through production systems:
-
Just-in-Time (JIT) Inventory: A cornerstone of pull through production, JIT aims to minimize inventory levels by receiving materials and producing goods only when needed. This significantly reduces storage costs, waste from obsolete stock, and the risk of holding onto unsold products.
-
Demand-Driven Production: The production process is initiated and paced by actual customer orders or demand signals. This dynamic approach ensures that resources are not wasted on unnecessary production.
-
Kanban System: Often used in conjunction with JIT, Kanban is a visual signaling system that manages workflow and inventory. Cards or other visual cues trigger the production of specific items when inventory levels fall below a predetermined threshold.
-
Continuous Improvement (Kaizen): Pull through production is intrinsically linked to continuous improvement. Regular evaluation and adjustment of the system are essential to maximize efficiency and minimize waste.
-
Strong Communication & Collaboration: Effective pull through production requires seamless communication and collaboration throughout the supply chain, from suppliers to customers. This ensures accurate demand information and timely material delivery.
Discussion: The Interplay of Aspects in Pull Through Production
The successful implementation of pull through production relies on the harmonious interaction of these aspects. For instance, a robust Kanban system wouldn't function optimally without accurate demand forecasting and a well-defined JIT inventory strategy. Similarly, continuous improvement efforts must involve all stakeholders to identify and address bottlenecks in the production process. Consider a company producing custom-designed furniture. A pull through system ensures that materials are sourced and components are manufactured only after a customer order is received, minimizing waste from unsold, standard designs.
Pull Through Production and Lean Manufacturing Principles
Pull through production is deeply rooted in the principles of lean manufacturing, aiming to eliminate waste (muda) in all its forms. The seven types of waste traditionally identified in lean manufacturing—overproduction, waiting, transportation, over-processing, inventory, motion, and defects—are significantly reduced through the implementation of a pull system.
Lean Manufacturing Principle: Just-in-Time (JIT)
JIT, a core component of lean manufacturing, aligns perfectly with pull through production. By minimizing inventory levels and only producing what is needed, JIT eliminates the waste associated with excessive stock, storage costs, and obsolescence. This frees up capital and space, allowing for greater flexibility and responsiveness to changing market conditions.
Lean Manufacturing Principle: Value Stream Mapping
Value stream mapping (VSM) is a powerful tool used to visualize and analyze the entire flow of materials and information in a production process. By identifying bottlenecks and areas for improvement, VSM plays a vital role in optimizing pull through production systems.
Implementing Pull Through Production: Challenges and Considerations
While offering substantial benefits, implementing a pull through production system presents certain challenges:
Challenge: Accurate Demand Forecasting
Accurate demand forecasting is critical for effective pull through production. Inaccurate predictions can lead to stockouts or excess inventory, undermining the efficiency gains of the system.
Challenge: Supply Chain Collaboration
Establishing strong communication and collaboration throughout the supply chain is crucial. Suppliers must be responsive and reliable to ensure timely delivery of materials.
Challenge: System Flexibility
Pull through production systems must be flexible enough to handle variations in demand. This requires adaptable production processes and the ability to quickly adjust production schedules.
FAQ: Addressing Common Questions About Pull Through Production
FAQ Introduction
This section addresses frequently asked questions regarding the implementation and benefits of pull through production.
Questions & Answers
Q1: What is the difference between pull and push production?
A1: Push production relies on forecasts to produce goods in advance of demand, often leading to excess inventory. Pull production, conversely, produces goods only when demand is confirmed, minimizing waste.
Q2: Is pull through production suitable for all industries?
A2: While suitable for many industries, its effectiveness depends on factors such as demand predictability, product customization, and supply chain responsiveness. Industries with highly predictable demand and readily available materials tend to benefit most.
Q3: How can technology support pull through production?
A3: Enterprise resource planning (ERP) systems, automated material handling, and real-time data analytics can enhance the efficiency and responsiveness of pull through production.
Q4: What are the potential risks of implementing a pull through system?
A4: Potential risks include stockouts due to inaccurate demand forecasting, supply chain disruptions impacting material availability, and the need for significant upfront investment in technology and training.
Q5: How can I measure the success of a pull through system?
A5: Key performance indicators (KPIs) such as inventory turnover rate, lead time reduction, and on-time delivery performance can gauge the effectiveness of the implemented system.
Q6: What are the initial steps in implementing a pull through system?
A6: Begin by assessing current processes, mapping the value stream, defining clear demand signals, and selecting appropriate technologies. Start with a pilot program in a limited area before scaling it across the entire operation.
Summary
Understanding the nuances of pull and push production is key to successful implementation.
Transition
The following section provides practical tips to successfully implement a pull-through production system.
Tips for Successful Pull Through Production Implementation
Tips Introduction
These tips offer actionable advice for companies seeking to successfully implement pull through production systems.
Tips
-
Conduct a thorough assessment of your current production process: Identify bottlenecks and areas of inefficiency before implementing any changes.
-
Invest in robust demand forecasting techniques: Utilize historical data, market analysis, and predictive modeling to minimize forecast inaccuracies.
-
Establish strong supplier relationships: Ensure your suppliers can consistently meet your just-in-time delivery requirements.
-
Implement a visual management system (e.g., Kanban): Improve communication and workflow visibility throughout the production process.
-
Employ lean principles to eliminate waste: Continuously identify and remove non-value-added activities.
-
Invest in appropriate technology: ERP systems, automated material handling, and real-time data analytics can optimize efficiency.
-
Train your employees: Provide comprehensive training to ensure all employees understand their roles and responsibilities in the pull through system.
-
Continuously monitor and improve: Track key performance indicators (KPIs) and make adjustments as needed.
Summary
By following these tips, companies can significantly increase the chances of successful pull through production implementation.
Transition
This article concludes by summarizing the key findings and offering a final perspective.
Summary of Pull Through Production
Pull through production represents a significant shift from traditional push production methods. By aligning production directly with customer demand, it minimizes waste, improves responsiveness, and enhances overall efficiency. Successful implementation requires a comprehensive understanding of lean principles, a commitment to continuous improvement, and strong collaboration throughout the supply chain.
Closing Message
The adoption of pull through production reflects a broader shift toward customer-centric manufacturing. By prioritizing agility and responsiveness, businesses can gain a competitive edge in today's dynamic market. The future of manufacturing lies in embracing adaptable and efficient production models, and pull through production offers a powerful pathway toward achieving this goal.
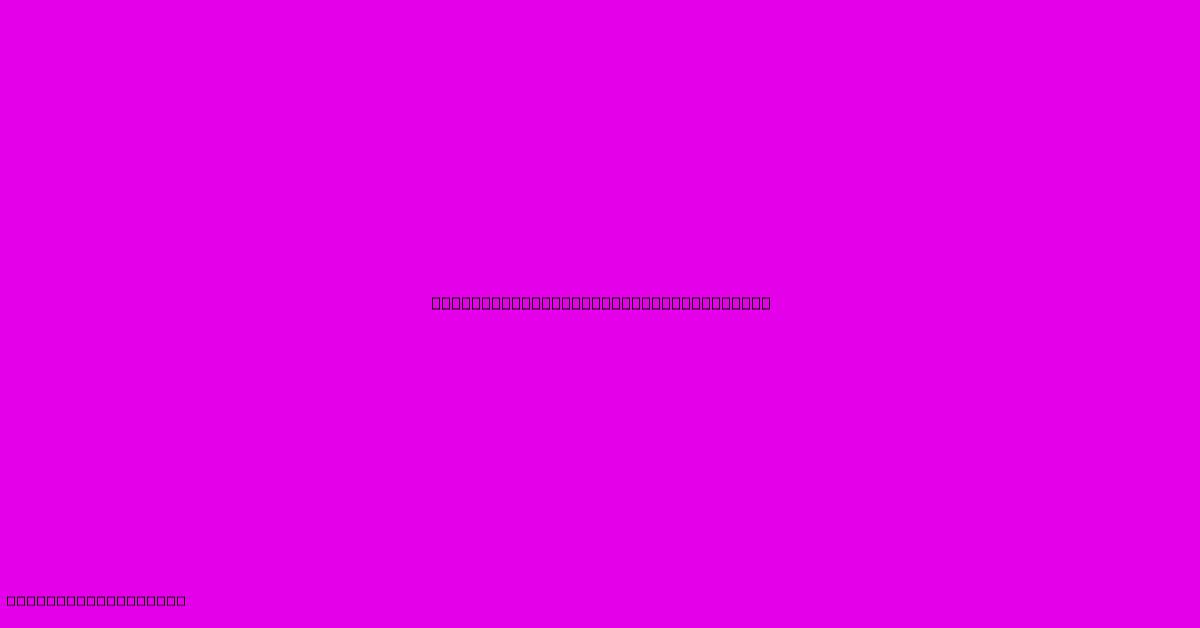
Thank you for taking the time to explore our website Pull Through Production Definition. We hope you find the information useful. Feel free to contact us for any questions, and don’t forget to bookmark us for future visits!
We truly appreciate your visit to explore more about Pull Through Production Definition. Let us know if you need further assistance. Be sure to bookmark this site and visit us again soon!
Featured Posts
-
What Is A Lender Credit
Jan 11, 2025
-
What Is Systemic Risk Definition In Banking Causes And Examples
Jan 11, 2025
-
B C Loan Definition
Jan 11, 2025
-
Static Budget Definition Limitations Vs A Flexible Budget
Jan 11, 2025
-
Terminal Value Tv Definition And How To Find The Value With Formula
Jan 11, 2025