Reserve Maintenance Period Definition
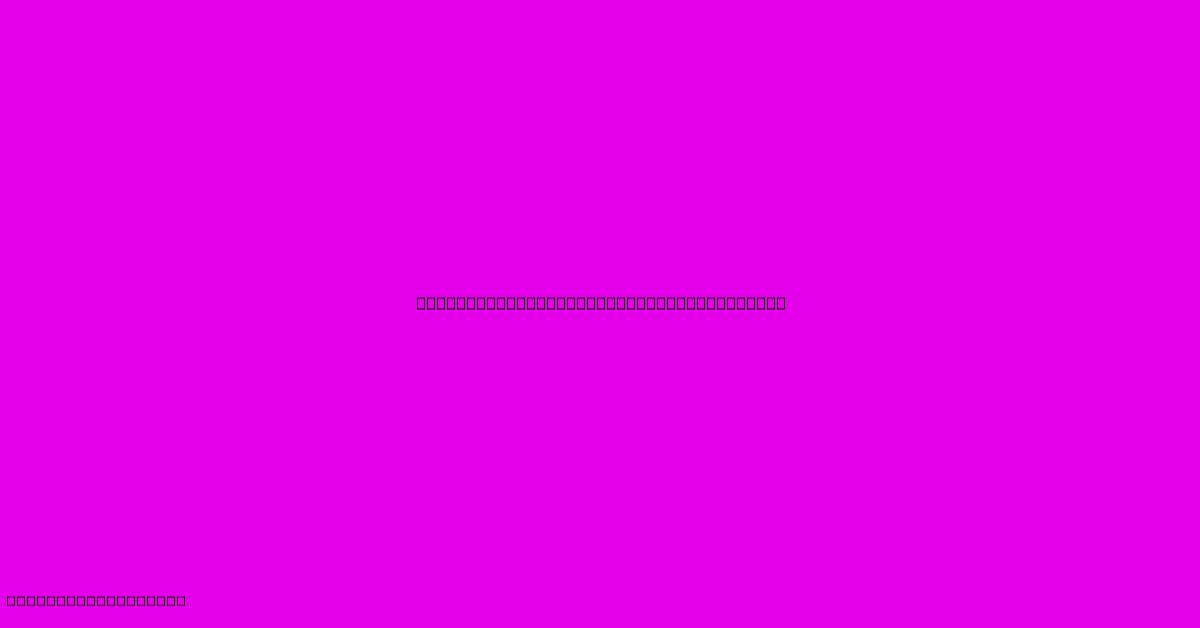
Discover more in-depth information on our site. Click the link below to dive deeper: Visit the Best Website meltwatermedia.ca. Make sure you don’t miss it!
Table of Contents
Unveiling Reserve Maintenance Periods: A Comprehensive Guide
Hook: What if your critical systems failed due to neglected maintenance? A robust reserve maintenance period strategy is crucial for minimizing downtime and maximizing operational efficiency.
Editor's Note: This comprehensive guide to Reserve Maintenance Periods has been published today.
Relevance & Summary: Understanding and effectively managing reserve maintenance periods is vital for any organization relying on complex systems. This guide explores the definition, planning, execution, and benefits of scheduling these crucial periods, covering aspects like risk assessment, resource allocation, and compliance. Semantic keywords include: reserve maintenance schedule, planned maintenance, preventative maintenance, downtime minimization, operational efficiency, risk mitigation, resource management, compliance, system reliability.
Analysis: This guide synthesizes industry best practices, regulatory guidelines, and real-world examples to provide a practical understanding of reserve maintenance periods. The information presented is based on established maintenance management principles and incorporates insights from various sources within the maintenance and operations management field.
Key Takeaways:
- Reserve maintenance periods are crucial for system longevity and optimal performance.
- Effective planning minimizes disruption and maximizes resource utilization.
- Risk assessment is paramount to identifying potential problems before they occur.
- Compliance with regulations ensures safety and operational legality.
- Regular review and adaptation are essential for continuous improvement.
Transition: Now, let's delve deeper into the critical aspects of reserve maintenance periods.
Reserve Maintenance Periods: A Deep Dive
Introduction: Reserve maintenance periods represent dedicated time slots allocated for performing preventative and corrective maintenance on critical systems or equipment. These periods are strategically planned to minimize disruption to ongoing operations while ensuring the long-term health and reliability of assets. The effectiveness of these periods significantly impacts operational efficiency, safety, and compliance with various regulations.
Key Aspects:
- Planning and Scheduling: This involves identifying critical assets, determining maintenance needs, and scheduling maintenance tasks to minimize conflicts and optimize resource allocation. Factors considered include the asset's criticality, the complexity of maintenance tasks, and the availability of skilled personnel and necessary parts.
- Risk Assessment and Mitigation: A thorough risk assessment identifies potential hazards associated with maintenance activities and develops mitigation strategies. This reduces the likelihood of accidents, injuries, or system failures during maintenance periods.
- Resource Allocation: Efficient allocation of personnel, tools, equipment, and materials is crucial for successful maintenance execution. This involves careful planning, clear communication, and coordination among various teams involved.
- Compliance and Documentation: Adherence to relevant safety regulations and standards is critical. Detailed documentation of all maintenance activities, including parts used, procedures followed, and any issues encountered, is crucial for auditing and future planning.
- Post-Maintenance Verification: After completing maintenance tasks, thorough verification is essential to ensure the system or equipment is functioning correctly and meets operational standards. This often includes testing and validation steps to confirm the success of the maintenance.
Understanding the Significance of Planned Maintenance
Introduction: Planned maintenance, a core component of reserve maintenance periods, focuses on preventative measures to prevent equipment failures and extend the lifespan of assets. Its significance is directly tied to reduced downtime, enhanced safety, and improved overall operational efficiency.
Facets:
- Role of Preventative Maintenance: Preventative maintenance involves regularly scheduled inspections, cleaning, lubrication, and component replacements to prevent equipment failures. This is a proactive approach that significantly reduces the likelihood of unexpected breakdowns.
- Examples of Preventative Tasks: This can include oil changes, filter replacements, lubrication of moving parts, inspections of electrical systems, and software updates. The specific tasks depend heavily on the nature of the asset.
- Risks and Mitigations of Preventative Maintenance: Inadequate planning, lack of skilled personnel, and insufficient resource allocation can hinder the effectiveness of preventative maintenance. Mitigations involve meticulous planning, proper training, and efficient resource management.
- Impacts and Implications of Effective Preventative Maintenance: Reduced downtime, extended equipment lifespan, increased safety, lower operational costs, and improved compliance are all positive impacts of well-executed preventative maintenance.
The Interplay Between Corrective Maintenance and Reserve Periods
Introduction: Corrective maintenance, addressing existing failures or malfunctions, also plays a vital role within reserve maintenance periods. The efficient integration of corrective maintenance with preventative measures ensures comprehensive system upkeep.
Further Analysis: Corrective maintenance activities often arise during inspections or as a result of identified issues. By incorporating these repairs into the reserve maintenance period, organizations can minimize disruptions caused by unexpected failures. Efficient scheduling ensures that these repairs do not extend the reserve maintenance period excessively. Examples include replacing a faulty component discovered during an inspection, or repairing a system that experienced a minor malfunction.
Closing: The strategic integration of corrective maintenance with planned preventative maintenance within defined reserve periods creates a holistic approach that optimizes resource utilization and minimizes disruptions, leading to enhanced operational efficiency and improved system reliability.
FAQ: Reserve Maintenance Periods
Introduction: This section addresses common questions regarding reserve maintenance periods.
Questions:
-
Q: What is the optimal frequency for reserve maintenance periods? A: The frequency depends on the criticality of the assets, their operating conditions, and industry best practices. Regular assessments are recommended.
-
Q: How are reserve maintenance periods planned? A: Planning involves identifying critical assets, assessing their maintenance needs, scheduling tasks, allocating resources, and coordinating with various teams.
-
Q: What if unforeseen issues arise during a reserve maintenance period? A: Contingency plans should be in place to address unexpected issues, potentially including extending the period or prioritizing critical repairs.
-
Q: How is the success of a reserve maintenance period measured? A: Success is measured by reduced downtime, improved system reliability, and adherence to safety standards and regulations.
-
Q: Are there regulatory requirements for reserve maintenance periods? A: This depends on the industry and specific assets, but many industries have regulations or guidelines regarding maintenance practices.
-
Q: What happens if a reserve maintenance period is not conducted properly? A: Improper execution can lead to increased downtime, safety hazards, equipment failures, and non-compliance issues.
Summary: Understanding and addressing common concerns ensures efficient management of reserve maintenance periods.
Transition: Let's now discuss practical tips for optimizing your reserve maintenance period strategy.
Tips for Optimizing Reserve Maintenance Periods
Introduction: These practical tips can enhance the effectiveness and efficiency of reserve maintenance period planning and execution.
Tips:
- Prioritize Critical Assets: Focus on assets critical to ongoing operations to minimize downtime risks.
- Utilize Predictive Maintenance Techniques: Incorporate data-driven analytics to anticipate potential failures and schedule maintenance proactively.
- Implement a Robust CMMS (Computerized Maintenance Management System): A CMMS streamlines scheduling, tracking, and reporting of maintenance activities.
- Invest in Skilled Personnel: Proper training and expertise are crucial for efficient and effective maintenance execution.
- Develop Contingency Plans: Address unexpected issues to minimize disruptions and maximize operational readiness.
- Regularly Review and Adapt: Continuously assess the effectiveness of the reserve maintenance strategy and make necessary adjustments.
- Maintain Clear Communication: Foster transparent communication among all teams involved to ensure coordinated efforts.
- Focus on Documentation: Comprehensive documentation supports audits, compliance, and future maintenance planning.
Summary: By incorporating these tips, organizations can significantly improve the efficiency and effectiveness of their reserve maintenance periods.
Transition: This guide concludes by summarizing the key takeaways and offering a final perspective.
Summary: Reserve Maintenance Period Management
Summary: This comprehensive guide explores the definition, planning, and execution of reserve maintenance periods, highlighting their importance for maintaining operational efficiency, ensuring system reliability, and minimizing downtime. Effective planning, risk assessment, resource allocation, and compliance with regulations are crucial for success.
Closing Message: Proactive and well-planned reserve maintenance periods are not just cost-saving measures; they are investments in operational resilience and business continuity. By embracing a robust maintenance strategy, organizations can build a foundation for sustained success and minimize the impact of potential system failures.
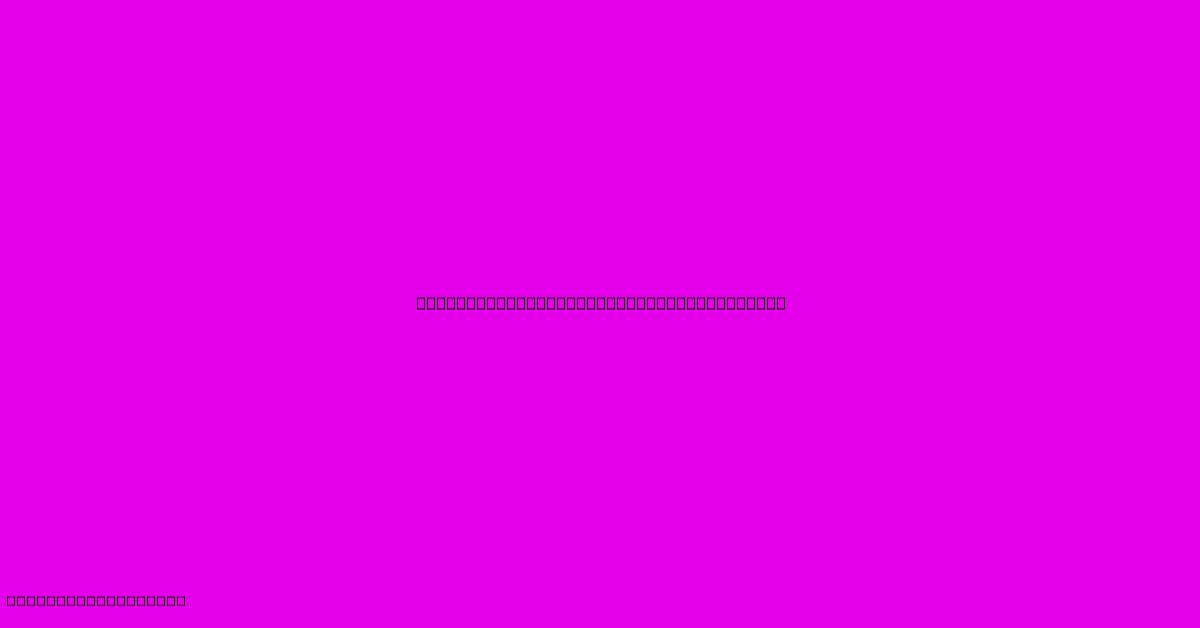
Thank you for taking the time to explore our website Reserve Maintenance Period Definition. We hope you find the information useful. Feel free to contact us for any questions, and don’t forget to bookmark us for future visits!
We truly appreciate your visit to explore more about Reserve Maintenance Period Definition. Let us know if you need further assistance. Be sure to bookmark this site and visit us again soon!
Featured Posts
-
What Stocks Pay Dividends Weekly
Jan 10, 2025
-
Revenue Passenger Mile Rpm Defining A Transportation Metric
Jan 10, 2025
-
How Much Money Do Pension Funds Have In The Stock Market
Jan 10, 2025
-
Why Are Shipping Stocks Down
Jan 10, 2025
-
What Is The Purpose Of Tax Planning
Jan 10, 2025