What Is A Prime Cost In Accounting
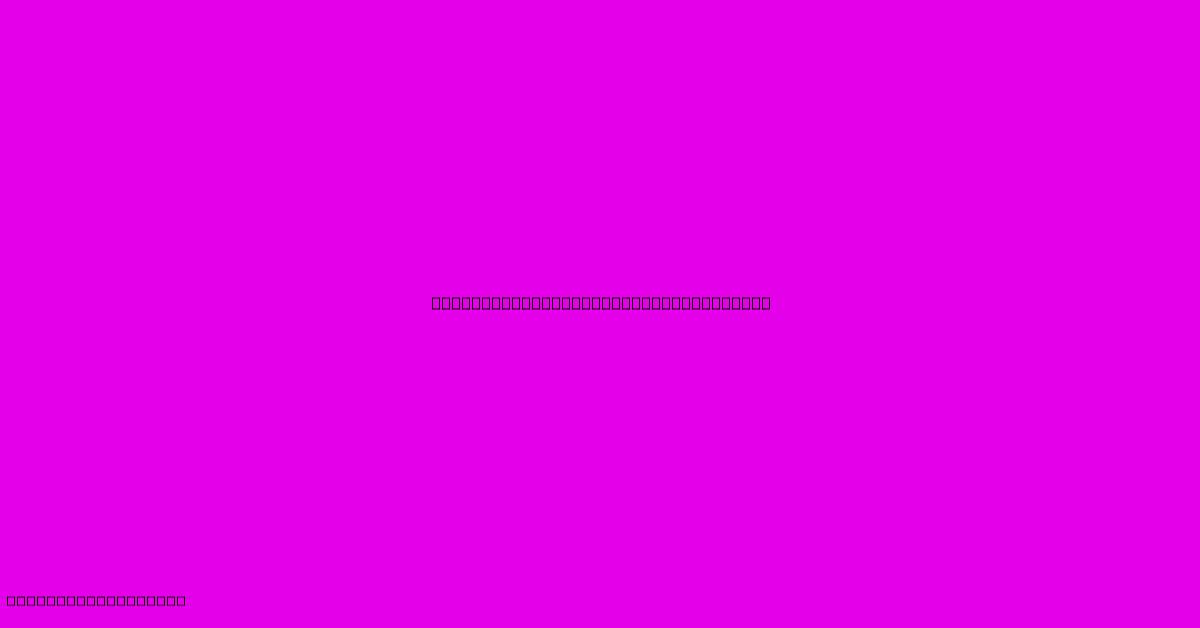
Discover more in-depth information on our site. Click the link below to dive deeper: Visit the Best Website meltwatermedia.ca. Make sure you don’t miss it!
Table of Contents
Unveiling Prime Cost: A Deep Dive into Accounting's Core Component
Hook: What single accounting metric most directly reflects the cost of producing goods? The answer, crucial for profitability analysis and pricing strategies, is prime cost.
Editor's Note: This comprehensive guide to prime cost in accounting has been published today.
Relevance & Summary: Understanding prime cost is vital for businesses of all sizes. This metric directly impacts pricing decisions, inventory valuation, and overall profitability assessments. This guide will explore the definition, components, calculation, and practical applications of prime cost, including its limitations and alternatives. Keywords used include: prime cost, direct costs, direct materials, direct labor, manufacturing overhead, cost accounting, product costing, cost of goods sold (COGS), profitability analysis, pricing strategy.
Analysis: This guide synthesizes established accounting principles and practical examples to provide a clear and concise explanation of prime cost. Information is drawn from reputable accounting textbooks and industry best practices.
Key Takeaways:
- Prime cost is the sum of direct materials and direct labor costs.
- It's a crucial element in determining the total cost of production.
- Understanding prime cost helps optimize pricing and improve profitability.
- Limitations exist, necessitating consideration of other cost elements.
Transition: Let's delve into a detailed exploration of prime cost and its significance in modern accounting practices.
Prime Cost: A Foundation of Cost Accounting
Introduction: Prime cost represents a fundamental building block in cost accounting. It directly reflects the resources consumed in the manufacturing process, providing a crucial insight into the core cost of production. Understanding its components and limitations is essential for accurate cost analysis and effective business decision-making.
Key Aspects: Prime cost is composed of two key elements: direct materials and direct labor.
Discussion:
Direct Materials
Introduction: Direct materials are raw materials that become an integral part of the finished product and can be directly traced to it.
Facets:
- Role: Forms the physical foundation of the product.
- Examples: Raw cotton in textile manufacturing, wood in furniture production, steel in automotive manufacturing.
- Risks & Mitigations: Price fluctuations, supply chain disruptions (mitigated through contracts, diverse sourcing).
- Impacts & Implications: Directly impacts the prime cost, influencing profitability and pricing decisions.
Direct Labor
Introduction: Direct labor comprises wages, salaries, and benefits paid to employees directly involved in the production process.
Facets:
- Role: Transforms raw materials into finished goods.
- Examples: Wages of assembly line workers, salaries of skilled craftsmen, benefits for production personnel.
- Risks & Mitigations: Labor shortages, wage increases (mitigated through training programs, automation).
- Impacts & Implications: Directly affects prime cost, influencing efficiency and overall production costs.
Summary: Both direct materials and direct labor are directly traceable to specific products, forming the core components of prime cost. Their accurate measurement is crucial for effective cost management and profitability assessment.
Prime Cost and its Relationship to Conversion Cost
Introduction: While prime cost focuses on the raw materials and direct labor involved in production, conversion cost highlights the transformation process itself.
Further Analysis: Conversion cost comprises direct labor and manufacturing overhead. Understanding the interplay between prime cost and conversion cost provides a more comprehensive view of total production costs. Analyzing the proportion of each cost element can reveal areas for efficiency improvements and cost reduction strategies. For instance, a high direct labor component might suggest opportunities for automation or process optimization, while high manufacturing overhead may point to inefficiencies in factory operations.
Closing: The relationship between prime cost and conversion cost underscores the need for a holistic approach to cost accounting. Analyzing both reveals a more complete picture of production expenses, facilitating better decision-making regarding pricing, production efficiency, and resource allocation.
Prime Cost vs. Total Cost
Introduction: Prime cost is a subset of total cost. Understanding the distinction is vital for accurate financial reporting and informed business decisions.
Further Analysis: Total cost encompasses all costs associated with production, including prime cost and manufacturing overhead. Manufacturing overhead includes indirect costs such as factory rent, utilities, and depreciation of machinery, which are not directly traceable to specific products. Accurate calculation of total cost is crucial for determining profitability, setting prices, and managing inventory.
Closing: While prime cost provides a crucial perspective on the direct costs of production, total cost provides a complete picture, encompassing all expenses incurred in manufacturing. A clear understanding of both is essential for informed business decisions.
FAQ: Prime Cost in Accounting
Introduction: This section addresses frequently asked questions about prime cost in accounting.
Questions:
-
Q: What is the difference between prime cost and cost of goods sold (COGS)? A: Prime cost is a component of COGS, representing only the direct materials and direct labor. COGS includes prime cost plus manufacturing overhead.
-
Q: How is prime cost used in pricing decisions? A: Businesses typically add a markup to the prime cost to cover overhead and achieve a desired profit margin.
-
Q: Can prime cost be negative? A: No, prime cost cannot be negative. It represents costs incurred, which are inherently positive.
-
Q: What are some limitations of using prime cost analysis? A: It does not include all costs of production (overhead), potentially leading to an incomplete picture of profitability.
-
Q: How does prime cost differ across industries? A: The proportion of direct materials and direct labor in prime cost varies significantly depending on the industry and production processes involved. Labor-intensive industries will have a larger direct labor component, while material-intensive industries will have a larger direct materials component.
-
Q: How can businesses reduce prime cost? A: This can be achieved through various means, including sourcing lower-cost materials, improving production efficiency to reduce labor costs, and negotiating better deals with suppliers.
Summary: Understanding these FAQs clarifies common misconceptions and provides a solid foundation for effective application of prime cost analysis.
Transition: Let’s move on to practical tips for managing and utilizing prime cost information effectively.
Tips for Effective Prime Cost Management
Introduction: Optimizing prime cost management is crucial for maximizing profitability.
Tips:
- Implement robust inventory management: Efficient inventory tracking minimizes waste and ensures materials are used effectively.
- Negotiate favorable supplier agreements: Secure better pricing and consistent supply chains.
- Invest in employee training: A skilled workforce enhances efficiency and reduces waste.
- Explore automation opportunities: Automating parts of the production process can lower labor costs.
- Regularly review and analyze prime cost data: Identify trends and potential areas for improvement.
- Benchmark against industry standards: Evaluate performance and identify best practices.
- Develop and use standard costing: This helps in setting targets and detecting variances.
Summary: These practical tips provide a framework for effective prime cost management, paving the way for increased efficiency and profitability.
Transition: Let’s summarize the key findings and implications of this analysis.
Summary: Understanding the Essence of Prime Cost
Summary: This comprehensive guide explored prime cost, its components (direct materials and direct labor), its calculation, and its applications in cost accounting. The relationship with conversion cost and total cost was analyzed, emphasizing the importance of a holistic cost accounting approach. Practical applications and strategies for managing prime cost effectively were discussed.
Closing Message: Mastering the concept of prime cost empowers businesses to make informed decisions about pricing, production, and resource allocation, ultimately driving profitability and long-term sustainability. Continuous monitoring and analysis of prime cost data are crucial for maintaining a competitive edge in today’s dynamic business environment.
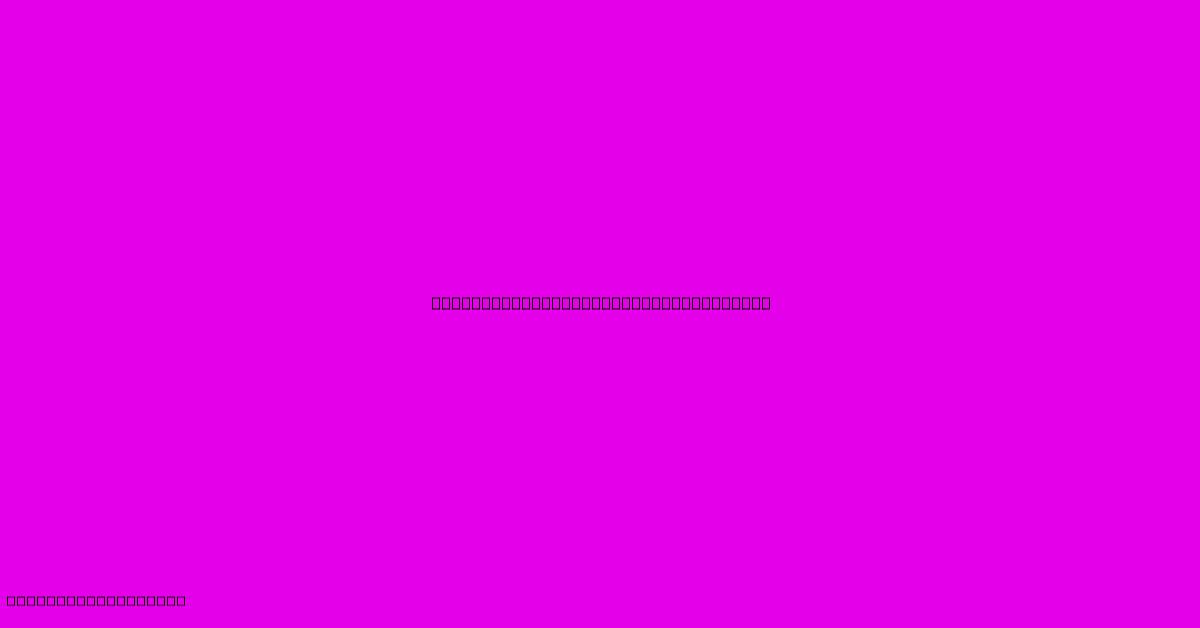
Thank you for taking the time to explore our website What Is A Prime Cost In Accounting. We hope you find the information useful. Feel free to contact us for any questions, and don’t forget to bookmark us for future visits!
We truly appreciate your visit to explore more about What Is A Prime Cost In Accounting. Let us know if you need further assistance. Be sure to bookmark this site and visit us again soon!
Featured Posts
-
Bankers Acceptance Ba Definition Meaning And Types
Jan 07, 2025
-
How Long Does It Take To Get A Life Insurance Policy
Jan 07, 2025
-
Why Is Dexilant Not Covered By Insurance
Jan 07, 2025
-
Federal Reserve Credit Definition
Jan 07, 2025
-
What Is The Purpose Of A Suicide Provision Within A Life Insurance Policy 2
Jan 07, 2025