What Is Purchase Order Lead Time Definition And How It Works
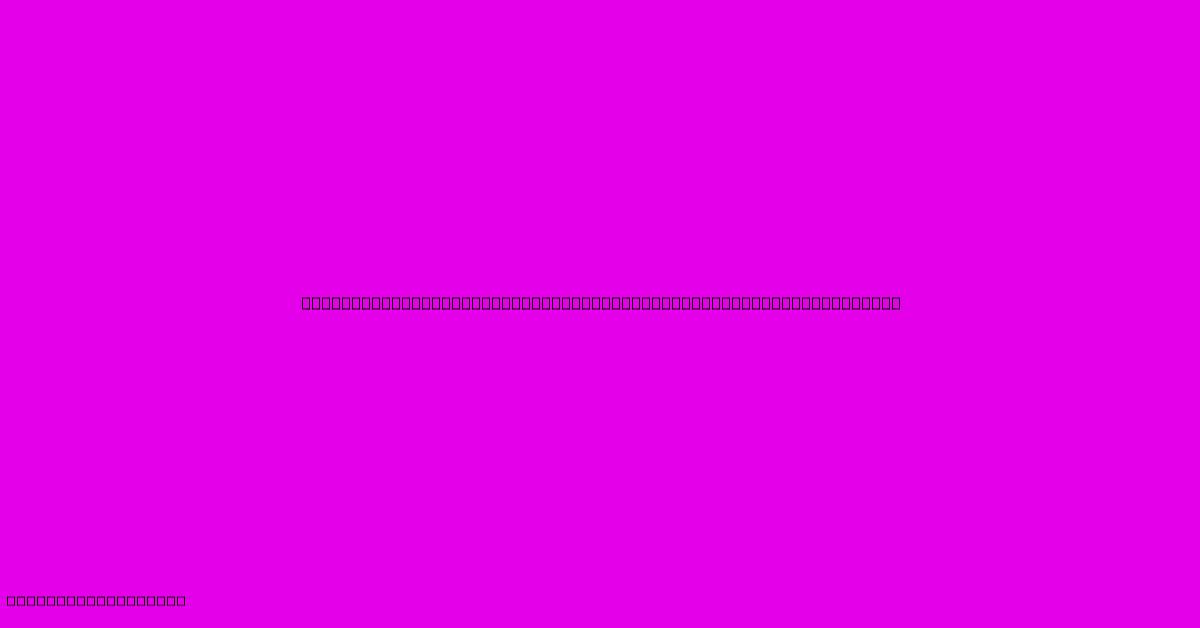
Discover more in-depth information on our site. Click the link below to dive deeper: Visit the Best Website meltwatermedia.ca. Make sure you don’t miss it!
Table of Contents
Unveiling Purchase Order Lead Time: A Comprehensive Guide
Hook: Does your business struggle with unpredictable delivery times? Understanding purchase order lead time is crucial for efficient inventory management and streamlined operations.
Editor's Note: This guide on Purchase Order Lead Time has been published today.
Relevance & Summary: Purchase order lead time significantly impacts a company's supply chain efficiency, profitability, and customer satisfaction. This comprehensive guide explores the definition, calculation, factors influencing it, and strategies for optimization. We'll cover key concepts like procurement, inventory management, and supply chain optimization to provide a holistic understanding. Understanding lead time allows for better forecasting, reduced stockouts, and improved overall business performance.
Analysis: This guide synthesizes research from industry best practices, supply chain management literature, and practical experiences to deliver actionable insights into managing purchase order lead time effectively. The information presented reflects established principles and strategies within the field of procurement and operations management.
Key Takeaways:
- Clear definition of purchase order lead time.
- Step-by-step calculation methods.
- Factors influencing lead time.
- Strategies for lead time reduction.
- Impact on inventory management and profitability.
Transition: Let's delve into a detailed explanation of purchase order lead time and its implications.
Purchase Order Lead Time: A Deep Dive
Introduction: Purchase order lead time (POLT) represents the timeframe between placing a purchase order with a supplier and receiving the goods or services. It's a critical metric in supply chain management, impacting everything from production scheduling to customer delivery promises. Understanding its components and influencing factors is essential for optimal business performance.
Key Aspects: POLT comprises several key stages: order placement, supplier processing, production, quality control, packaging, shipping, and finally, delivery. Each stage contributes to the overall lead time, and inefficiencies in any one area can significantly impact the total time.
Discussion:
Order Placement:
This initial phase involves the buyer creating and transmitting the purchase order. Factors affecting this stage include internal approval processes, the accuracy of order details, and the chosen communication method (e.g., email, EDI). Streamlining internal approvals and ensuring accurate order information can significantly shorten this phase.
Supplier Processing:
Once the order is received, the supplier begins processing it. This includes verifying the order details, checking inventory availability, and scheduling production. Supplier capacity, internal processes, and order volume all influence this stage. Collaborating closely with suppliers to understand their capacity and providing clear, consistent order information can improve efficiency.
Production:
This is typically the longest phase of the POLT, encompassing the manufacturing or production of the ordered goods. The complexity of the product, available resources (labor, machinery), and production scheduling all affect this stage. Effective production planning and lean manufacturing techniques can significantly reduce production lead time.
Quality Control:
After production, quality checks are performed to ensure the goods meet the specified requirements. Rigorous quality control can lead to delays, but it's crucial for maintaining product quality and customer satisfaction. Implementing efficient quality control procedures and proactive defect prevention strategies can minimize delays without compromising quality.
Packaging and Shipping:
Packaging the goods appropriately and selecting a suitable shipping method are vital. Packaging efficiency and shipping carrier reliability are key factors here. Optimizing packaging processes and partnering with reliable shipping providers can contribute to faster delivery.
Delivery:
The final stage involves transporting the goods from the supplier to the buyer. Transportation time depends on geographical distance, chosen shipping method, and traffic conditions. Efficient logistics and planning, including selecting appropriate transportation modes and routes, are key.
Factors Influencing Purchase Order Lead Time
Several factors influence the length of a purchase order lead time. These include:
- Supplier Capacity: A supplier’s production capacity and current workload directly impact how quickly they can fulfill orders. Overburdened suppliers often lead to longer lead times.
- Order Complexity: Complex orders with unique specifications or customizations require more time to process and manufacture.
- Distance: The geographical distance between the buyer and supplier significantly impacts shipping time.
- Seasonality: Demand fluctuations due to seasonality can affect lead times, as suppliers might experience increased workloads during peak seasons.
- Inventory Levels: Suppliers with sufficient inventory can fulfill orders faster than those with low stock levels.
- Transportation: Reliable and efficient transportation plays a crucial role in the delivery phase. Delays due to logistics can significantly impact the overall lead time.
- Technology: Implementing advanced technologies, like Enterprise Resource Planning (ERP) systems and supply chain management software, can streamline processes and reduce lead times.
- Communication: Clear and effective communication between buyer and supplier ensures timely resolution of issues and minimizes delays.
Strategies for Reducing Purchase Order Lead Time
Reducing POLT requires a multi-faceted approach encompassing improvements across the entire supply chain. Here are some strategies:
- Supplier Relationship Management: Building strong relationships with key suppliers enables better collaboration, information sharing, and faster issue resolution.
- Inventory Optimization: Implementing robust inventory management systems helps maintain adequate stock levels while avoiding excess inventory. This ensures that suppliers have the necessary materials readily available.
- Lean Manufacturing Principles: Adopting lean manufacturing techniques helps streamline production processes, reduce waste, and improve efficiency.
- Technology Implementation: Integrating advanced technologies can automate processes, improve communication, and enhance visibility throughout the supply chain.
- Demand Forecasting: Accurate demand forecasting allows businesses to anticipate future needs and place orders proactively, mitigating potential delays.
- Strategic Sourcing: Carefully selecting suppliers based on factors like lead time, capacity, and reliability is essential for optimizing the entire process.
The Impact of Purchase Order Lead Time
Effective management of purchase order lead time has a significant impact on various aspects of a business:
- Inventory Management: Accurate lead time prediction is crucial for maintaining optimal inventory levels, minimizing storage costs, and preventing stockouts.
- Production Scheduling: Reliable lead time data allows for accurate production scheduling, ensuring timely completion of projects and meeting customer deadlines.
- Customer Satisfaction: Consistent and predictable delivery times lead to improved customer satisfaction and loyalty.
- Profitability: Efficient lead time management reduces inventory holding costs, minimizes stockouts, and improves operational efficiency, ultimately boosting profitability.
FAQ
Introduction: This section addresses common questions about purchase order lead time.
Questions:
-
Q: How is purchase order lead time calculated? A: It's calculated by subtracting the purchase order date from the date goods are received.
-
Q: What is the difference between lead time and cycle time? A: Lead time focuses on the time from order to delivery, while cycle time is the time it takes to complete a single unit of production.
-
Q: How can I track purchase order lead time? A: Utilize software systems, spreadsheets, or dedicated supply chain management tools.
-
Q: What are the consequences of long purchase order lead times? A: Stockouts, increased inventory costs, production delays, and dissatisfied customers.
-
Q: How can I negotiate shorter lead times with my suppliers? A: Build strong relationships, provide accurate forecasts, and offer incentives.
-
Q: What is the role of technology in optimizing POLT? A: Automation, data analytics, and real-time tracking improve efficiency and predictability.
Summary: Understanding and managing POLT effectively requires continuous monitoring, collaboration with suppliers, and implementing best practices.
Transition: Let’s explore some practical tips for optimizing POLT.
Tips for Optimizing Purchase Order Lead Time
Introduction: This section provides actionable steps for improving your purchase order lead time.
Tips:
- Establish clear communication channels: Maintain open and constant communication with your suppliers.
- Implement a robust inventory management system: Use software to track inventory levels and forecast demand accurately.
- Negotiate favorable payment terms: Incentivize suppliers to prioritize your orders.
- Regularly review supplier performance: Identify areas for improvement and potential risks.
- Diversify your supply base: Reduce reliance on a single supplier to mitigate risk.
- Invest in technology: Use ERP systems and supply chain management tools to streamline processes.
- Develop strong supplier relationships: Build trust and collaboration for efficient problem-solving.
- Conduct regular lead time analysis: Identify bottlenecks and areas for improvement.
Summary: By implementing these tips, businesses can significantly reduce their purchase order lead times, improve efficiency, and enhance profitability.
Transition: Let's conclude our exploration of purchase order lead time.
Summary of Purchase Order Lead Time
This comprehensive guide has explored the definition, calculation, and influencing factors of purchase order lead time. We've also examined strategies for optimizing lead times and highlighted its impact on various aspects of a business. Understanding and managing POLT effectively is crucial for successful supply chain management.
Closing Message: Proactive management of purchase order lead time is not merely a cost-saving measure; it's a strategic imperative for enhancing operational efficiency, improving customer satisfaction, and driving overall business success. By focusing on process improvements, supplier collaboration, and technology integration, businesses can achieve significant gains in agility and profitability. Continuous monitoring and adaptation are crucial in the ever-evolving world of supply chain management.
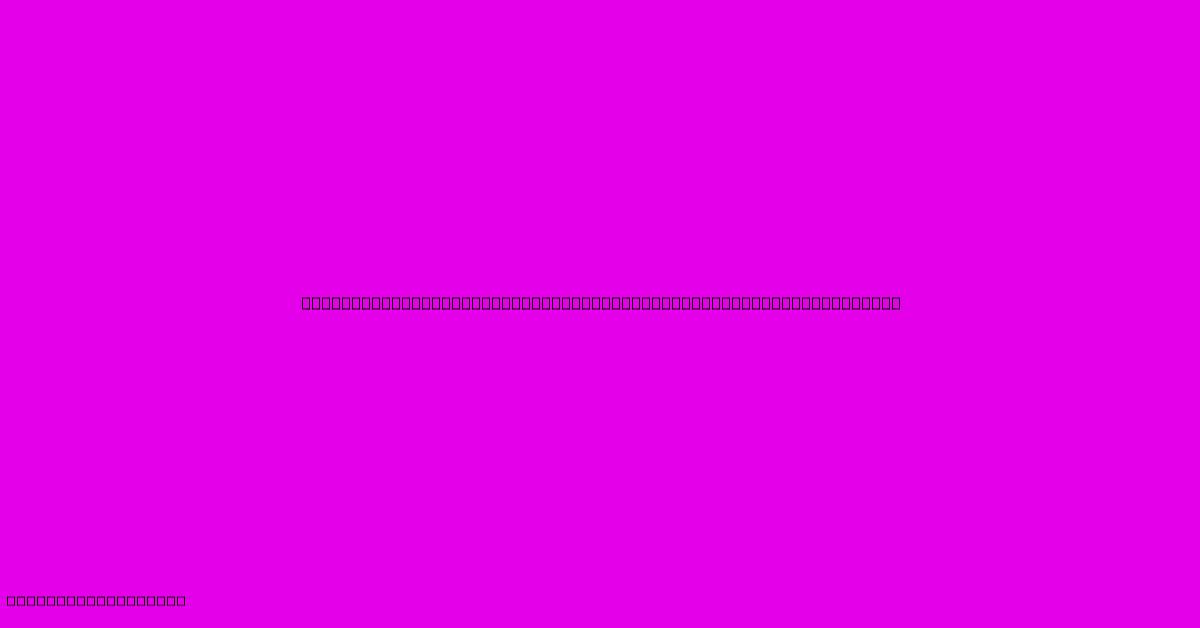
Thank you for taking the time to explore our website What Is Purchase Order Lead Time Definition And How It Works. We hope you find the information useful. Feel free to contact us for any questions, and don’t forget to bookmark us for future visits!
We truly appreciate your visit to explore more about What Is Purchase Order Lead Time Definition And How It Works. Let us know if you need further assistance. Be sure to bookmark this site and visit us again soon!
Featured Posts
-
What Is Ach Credit
Jan 12, 2025
-
In What Ways Are Joint Ventures And Syndicates Alike
Jan 12, 2025
-
Why Do Insurance Companies Use Letters Of Credit
Jan 12, 2025
-
What Is Credit Protection Credit One
Jan 12, 2025
-
What Is A Tip Credit On My Paycheck
Jan 12, 2025