What To Do When Taking Inventory In A Small Business
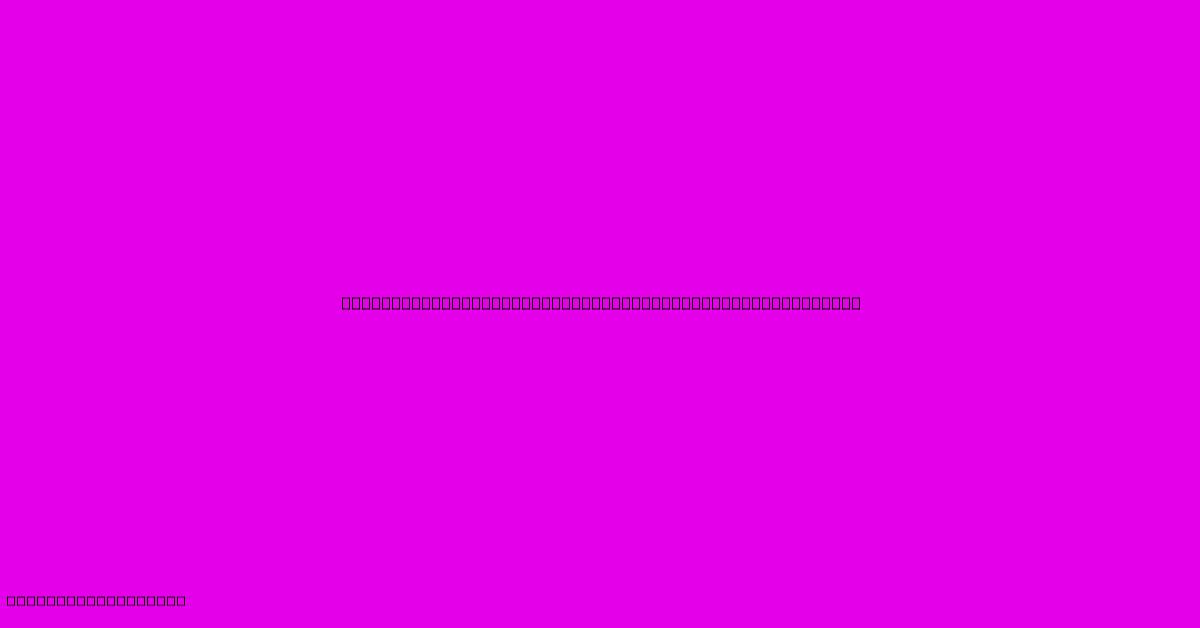
Discover more in-depth information on our site. Click the link below to dive deeper: Visit the Best Website meltwatermedia.ca. Make sure you don’t miss it!
Table of Contents
Mastering Inventory: A Small Business Guide to Accurate Stocktaking
Does accurate inventory management feel like a Herculean task for your small business? A robust inventory system is the backbone of profitability. This comprehensive guide provides a clear, informative strategy for efficient and accurate stocktaking, enabling informed decisions and boosting your bottom line.
Editor's Note: This guide to effective inventory management for small businesses has been published today.
Relevance & Summary: Maintaining precise inventory levels is crucial for small businesses. Overstocking ties up capital and risks obsolescence, while understocking leads to lost sales and dissatisfied customers. This guide outlines essential steps, from preparation to reconciliation, to streamline your inventory process, minimizing errors and maximizing efficiency. Key aspects include planning, physical counting, data entry, and reconciliation, utilizing techniques applicable to various inventory systems (e.g., manual, spreadsheet-based, or software-driven).
Analysis: This guide draws on established inventory management best practices, incorporating insights from industry experts and case studies of successful small businesses. It emphasizes a methodical approach, highlighting the importance of accuracy and efficient data handling to minimize errors and reduce operational costs.
Key Takeaways:
- Thorough preparation is paramount.
- Accurate counting techniques minimize errors.
- Efficient data entry speeds up the process.
- Reconciliation identifies discrepancies and improves accuracy.
- Regular stocktaking maintains inventory accuracy.
What to Do When Taking Inventory in a Small Business
Introduction: Effective inventory management is a cornerstone of small business success. This section details the crucial steps involved in conducting a complete and accurate inventory, ensuring efficient operations and informed decision-making.
Key Aspects of Inventory Taking:
This process can be broken down into several key stages: planning, physical counting, data entry, and reconciliation. Each step is vital for ensuring accuracy and minimizing disruption to your business operations.
Discussion:
1. Planning Your Inventory:
Before starting the physical count, meticulous planning is critical. This involves several key aspects:
-
Scheduling: Choose a period of low business activity to minimize disruption. Weekends or slow business days are ideal. Communicate the chosen dates to all staff involved, ensuring everyone understands the schedule.
-
Team Formation: Assign roles and responsibilities clearly. Different team members can be responsible for specific areas or product categories. Designate a team leader to oversee the process, ensuring smooth coordination and resolving any issues.
-
Supplies: Gather necessary supplies: barcode scanners (if applicable), tally sheets, pens, clipboards, and possibly additional lighting for dimly lit storage areas. Prepare sufficient forms for recording inventory data. If using a spreadsheet or software, ensure it is functioning correctly and accessible to all team members. Backups are essential!
-
Preparation of Inventory Lists: If using a digital inventory management system, ensure all items are accurately reflected in the system. If relying on physical lists, verify their accuracy and completeness against existing stock. Categorize items to expedite counting and organize your data.
2. Physical Counting:
This is the core of the inventory process:
-
Counting Procedures: Employ systematic methods for counting. Moving along a logical route, such as starting at one end of the warehouse or shelf and working methodically through each area, prevents double-counting or missed items. Use consistent units of measure (e.g., pieces, dozens, cases).
-
Accuracy Techniques: Use a two-person counting system, having one person count and another record the results. Double-checking quantities is crucial to minimize errors. For high-value items, consider additional checks by different team members.
-
Handling Discrepancies: Immediately document any damaged, missing, or misplaced items. Note the quantity and condition of any discrepancies. Take photographs to support findings. This aids in the identification of potential issues, like theft or damage.
-
Proper Identification: Make sure that items are correctly identified. Use barcodes or clear labels whenever possible for easier tracking.
3. Data Entry:
Once the physical count is complete, accurate data entry is crucial:
-
Data Entry Methods: If using a manual system, ensure legible handwriting. Use spreadsheets or inventory software for better accuracy and reporting. Import barcode data to eliminate manual entry and reduce errors.
-
Error Prevention: Regularly check data entries for accuracy. Use cross-referencing to validate data against physical count sheets.
4. Reconciliation:
This final step compares the physical count results with existing inventory records:
-
Variance Analysis: Identify discrepancies between the physical count and recorded inventory levels. Investigate the reasons behind any significant differences.
-
Adjustments: Make necessary adjustments to your inventory records to reflect the accurate quantities. Record all adjustments with a clear explanation.
-
Reporting: Generate reports to highlight variances and summarize the findings. These reports provide valuable insights into your inventory management processes and help identify areas for improvement.
Inventory Management Software
Using inventory management software drastically simplifies stocktaking. Many programs allow for barcode scanning, reducing data entry errors and accelerating the process. Software also typically offers features for generating reports, analyzing inventory trends, and setting reorder points.
Regular Stocktaking:
Regular stocktaking, even if less comprehensive than a full annual inventory, helps to maintain inventory accuracy. This might involve counting specific high-demand items or reviewing stock levels more frequently. Regular spot checks can catch discrepancies before they become major problems.
FAQ
Introduction: This section addresses frequently asked questions about inventory management for small businesses.
Questions:
-
Q: How often should I take a full inventory? A: The frequency depends on the nature of your business and inventory turnover rate. Annual inventories are common, but more frequent counts might be necessary for businesses with high-value or perishable goods.
-
Q: What if I discover significant discrepancies? A: Investigate the reasons for the discrepancies. Review your inventory management processes to identify potential weaknesses. Consider implementing stricter controls to prevent future discrepancies.
-
Q: What software is best for inventory management? A: Numerous inventory management software options exist for small businesses. Consider features like barcode scanning, reporting, and integration with other business systems.
-
Q: Can I outsource my inventory taking? A: Yes, many inventory management services can handle stocktaking for your business. This can be a cost-effective solution, particularly for businesses with large or complex inventories.
-
Q: What is the role of cycle counting in inventory management? A: Cycle counting is a method of counting a small subset of your inventory regularly, rather than a full count annually. It helps prevent discrepancies from becoming too large.
-
Q: How can I minimize inventory shrinkage? A: Improve security, implement better tracking systems, and address any issues with damage or spoilage.
Summary: Accurate inventory management is essential for the success of any small business. Regular stocktaking, coupled with effective inventory management practices, leads to increased efficiency and profitability.
Tips for Effective Inventory Management
Introduction: This section provides practical tips to streamline your inventory management processes and improve accuracy.
Tips:
-
Use a Consistent System: Implement a standardized method for recording and tracking inventory across all departments.
-
Regularly Review Stock Levels: Analyze sales data and consumption patterns to identify items that are overstocked or understocked.
-
Implement a Reorder Point System: Determine reorder points for each item to ensure timely replenishment of stock.
-
Train Employees Properly: Ensure that all employees involved in inventory management understand the procedures and are trained to use any necessary technology.
-
Utilize Technology: Consider using barcode scanners, inventory management software, or other technological tools to improve accuracy and efficiency.
-
Regularly Audit Your Inventory Management Process: Periodic reviews can pinpoint inefficiencies and areas for improvement.
-
Conduct Physical Inventory Checks Regularly: Regular spot-checks or cycle counting can help prevent major discrepancies from developing.
-
Store Items Properly: Proper storage reduces damage and prevents loss of inventory.
Summary: These tips, when implemented effectively, will significantly improve your inventory management processes, resulting in reduced errors, optimized stock levels, and increased profitability.
Summary: Mastering Inventory Management in Your Small Business
This guide provides a comprehensive approach to accurate inventory management for small businesses. By meticulously planning, accurately counting, efficiently entering data, and diligently reconciling results, businesses can ensure inventory records are accurate, reflecting the true state of their stock. Implementing the techniques described above will minimize errors, optimize stock levels, and ultimately contribute to improved profitability and efficiency. Utilizing technology and establishing clear processes leads to smoother operations and more informed business decisions.
Closing Message: Investing time and effort in mastering inventory management is an investment in your small business's future success. Consistent attention to detail and the implementation of robust procedures will not only improve accuracy but also unlock valuable insights that inform effective purchasing, pricing, and overall business strategy. Remember, accurate inventory data underpins successful business operations.
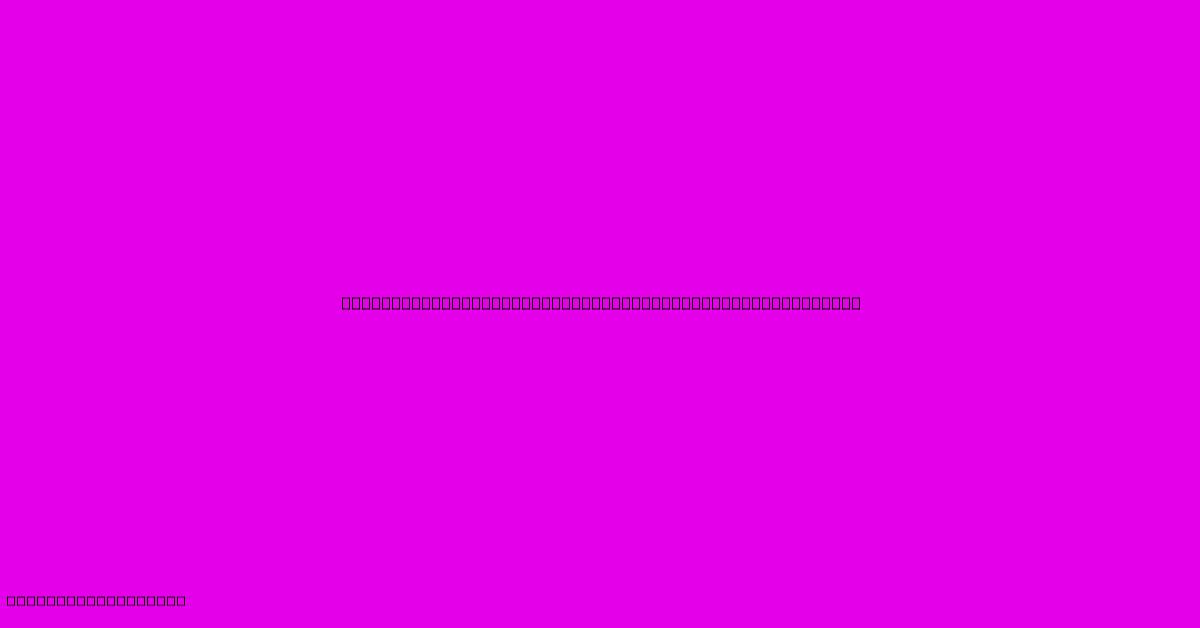
Thank you for taking the time to explore our website What To Do When Taking Inventory In A Small Business. We hope you find the information useful. Feel free to contact us for any questions, and don’t forget to bookmark us for future visits!
We truly appreciate your visit to explore more about What To Do When Taking Inventory In A Small Business. Let us know if you need further assistance. Be sure to bookmark this site and visit us again soon!
Featured Posts
-
How Much Is Gabapentin Without Insurance
Jan 07, 2025
-
What Is The Replacement Rule In Life Insurance
Jan 07, 2025
-
How Much Is Livery Insurance
Jan 07, 2025
-
How Much Is Homeowners Insurance Georgia
Jan 07, 2025
-
How Much Is Full Coverage Insurance In Michigan
Jan 07, 2025