Capacity Requirements Planning Crp Definition And Procedures
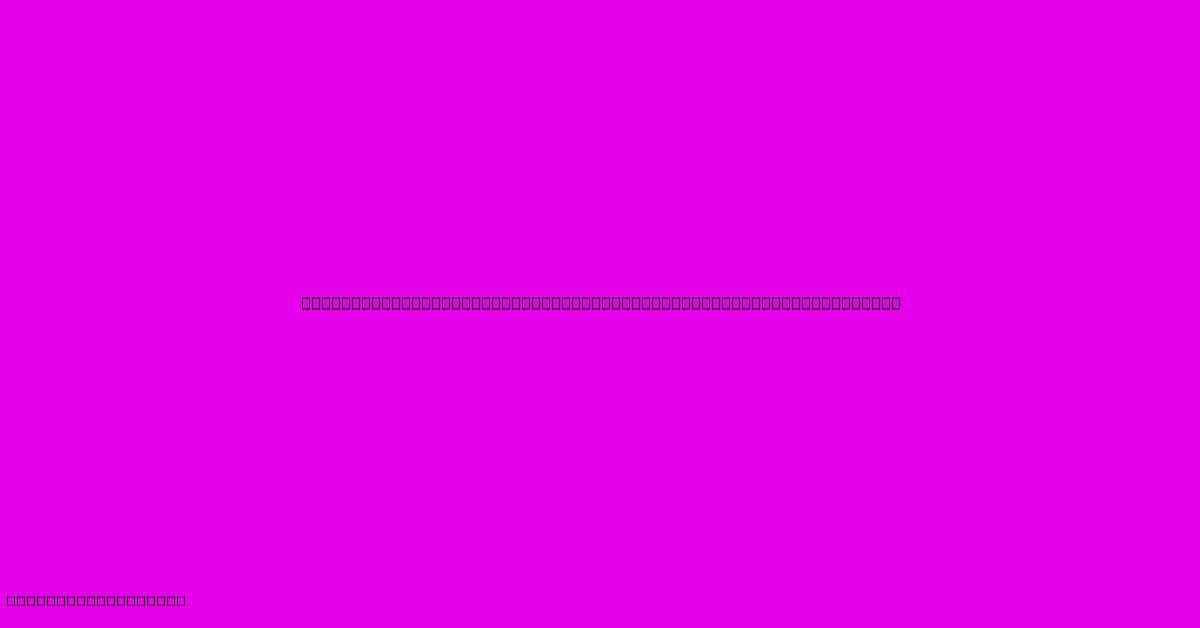
Discover more in-depth information on our site. Click the link below to dive deeper: Visit the Best Website meltwatermedia.ca. Make sure you don’t miss it!
Table of Contents
Unveiling Capacity Requirements Planning (CRP): A Comprehensive Guide
Hook: Does your manufacturing process consistently meet deadlines and efficiently utilize resources? A robust Capacity Requirements Planning (CRP) system is crucial for avoiding costly production bottlenecks and ensuring on-time delivery.
Editor's Note: This comprehensive guide to Capacity Requirements Planning (CRP) was published today.
Relevance & Summary: Capacity Requirements Planning (CRP) is a crucial production planning and control technique that ensures manufacturing facilities have the necessary resources—equipment, labor, and materials—to meet forecasted production demands. This guide explores the definition, procedures, benefits, and challenges of CRP, providing a detailed understanding of its importance in achieving operational efficiency and profitability. We'll delve into key concepts like workload calculations, capacity analysis, and the integration of CRP with other production planning tools like Material Requirements Planning (MRP). Semantic keywords include: capacity planning, resource planning, production planning, manufacturing, workload, bottleneck analysis, scheduling, efficiency, optimization, MRP integration.
Analysis: This guide draws upon established literature in production and operations management, best practices from various industries, and real-world case studies to offer a practical and insightful overview of Capacity Requirements Planning.
Key Takeaways:
- CRP ensures sufficient resources for meeting production schedules.
- It helps identify and mitigate potential production bottlenecks.
- CRP enhances production efficiency and reduces lead times.
- Effective CRP improves on-time delivery performance.
- It facilitates better resource allocation and utilization.
Capacity Requirements Planning (CRP)
Introduction
Capacity Requirements Planning (CRP) is a vital production planning and control technique used to determine whether sufficient resources—including labor, machines, and materials—are available to meet the demands of a production schedule. It bridges the gap between the master production schedule (MPS) and the actual execution of production, ensuring that production plans are feasible and realistic. Understanding and implementing CRP effectively can significantly impact a company's competitiveness by reducing lead times, improving on-time delivery, and optimizing resource utilization.
Key Aspects of CRP
CRP involves several critical aspects that contribute to its overall effectiveness:
- Forecasting: Accurate demand forecasting forms the foundation of CRP. Reliable forecasts of customer orders are essential for generating a realistic master production schedule (MPS).
- Master Production Schedule (MPS): The MPS serves as the input for CRP, detailing the planned production quantities for each product over a specific time horizon.
- Capacity Requirements: This involves calculating the required capacity for each resource (machines, labor, etc.) based on the MPS and the bill of materials (BOM). This usually requires detailed routing information.
- Capacity Availability: This step involves assessing the available capacity for each resource, taking into account factors such as machine downtime, employee absences, and other potential constraints.
- Capacity Planning: This involves comparing capacity requirements with capacity availability to identify potential bottlenecks or capacity shortfalls.
- Resource Allocation and Scheduling: Based on the capacity analysis, resources are allocated to specific tasks and scheduled to optimize production efficiency.
- Monitoring and Control: Ongoing monitoring of actual production against the planned schedule is necessary to identify and address any deviations from the plan.
Discussion
Each aspect of CRP is crucial for its success. Let's examine them in more detail:
Forecasting: Inaccurate demand forecasts can lead to either underutilization or overutilization of resources. Sophisticated forecasting techniques, such as moving averages, exponential smoothing, and time series analysis, can improve forecast accuracy.
Master Production Schedule (MPS): The MPS is the foundation upon which CRP is built. A well-defined MPS, carefully considering customer orders, inventory levels, and production capabilities, is essential for generating accurate capacity requirements.
Capacity Requirements and Availability: These are determined through a detailed analysis of the production process, considering machine run times, setup times, labor requirements per unit, and other relevant factors. Capacity availability needs to take into account scheduled maintenance, planned downtime, and employee holidays.
Capacity Planning: Identifying capacity shortfalls or bottlenecks is critical. Solutions can include increasing resource availability (e.g., purchasing new equipment, hiring additional staff), adjusting the MPS, or outsourcing certain production activities.
Resource Allocation and Scheduling: Once capacity requirements and availability are analyzed, resources need to be carefully allocated and scheduled to meet production demands efficiently. Sophisticated scheduling techniques, like Finite Capacity Scheduling (FCS), can optimize resource utilization and minimize lead times.
Monitoring and Control: Real-time monitoring of actual production against the planned schedule is crucial. This allows for timely identification and resolution of any discrepancies, preventing them from escalating into major production disruptions.
CRP Procedures
CRP procedures typically involve the following steps:
- Data Collection: Gathering necessary data such as the MPS, BOM, routing information, resource availability, and labor standards.
- Capacity Requirements Calculation: Using the collected data to calculate the capacity required for each resource to fulfill the MPS. This often involves calculating workload using standard times per operation.
- Capacity Availability Analysis: Determining the available capacity for each resource, accounting for downtime, maintenance, and other constraints.
- Capacity Gap Identification: Comparing capacity requirements with capacity availability to identify any potential capacity shortages or bottlenecks.
- Action Planning: Developing and implementing plans to address capacity gaps, which may include adjustments to the MPS, overtime scheduling, or acquiring additional resources.
- Implementation and Monitoring: Implementing the adjusted production plan and closely monitoring actual production against the planned schedule to make adjustments as needed.
Workload and Bottleneck Analysis within CRP
Introduction
Workload and bottleneck analysis are critical components of effective CRP. They help identify potential constraints within the production process and ensure that the available capacity is efficiently utilized.
Facets:
- Workload Calculation: Determining the total workload for each resource based on the planned production schedule and the resource requirements for each operation. This often involves calculating the total processing time needed for each resource across all planned production.
- Bottleneck Identification: Identifying the resource(s) with the lowest capacity, which may become a bottleneck, limiting overall production output. This may include analyzing machine capacity, labor hours, or material availability.
- Bottleneck Analysis: Investigating the reasons behind a bottleneck. This could stem from inadequate equipment, insufficient skilled labor, material shortages, or inefficient processes.
- Bottleneck Mitigation: Strategies for addressing bottlenecks may involve investing in additional capacity, improving process efficiency, rescheduling production, or outsourcing certain tasks.
- Impact and Implications: Unidentified and unaddressed bottlenecks significantly impact on-time delivery, increase lead times, and negatively affect overall production efficiency.
Summary
Effective workload and bottleneck analysis is crucial for successful CRP implementation. By identifying and addressing potential constraints proactively, companies can significantly improve production efficiency, optimize resource utilization, and meet production demands on time and within budget.
Integrating CRP with MRP
Introduction
Integrating CRP with Material Requirements Planning (MRP) strengthens the overall production planning process. MRP focuses on material availability, while CRP addresses capacity constraints. The combined approach ensures both the materials and the resources are available for the planned production.
Further Analysis
By integrating both systems, businesses gain a holistic view of their production process, leading to more accurate planning and improved efficiency. This synergistic approach improves forecast accuracy, reduces inventory holding costs, and enhances overall production performance. Early identification of potential capacity shortfalls allows for proactive adjustments to the MPS and material orders, preventing delays and reducing production disruptions.
Closing
The combined use of MRP and CRP creates a robust production planning system that mitigates risks and optimizes resource allocation. This integrated approach significantly enhances production efficiency and supports better decision-making.
FAQ
Introduction
This section answers frequently asked questions about Capacity Requirements Planning.
Questions:
- Q: What is the difference between CRP and MRP? A: MRP focuses on ensuring sufficient materials are available for production, while CRP focuses on ensuring sufficient capacity (labor, machines, etc.) to process those materials.
- Q: How often should CRP be performed? A: The frequency depends on factors such as the production cycle time and the volatility of demand. It can be performed weekly, monthly, or even continuously for real-time monitoring.
- Q: What are the common challenges in implementing CRP? A: Challenges include accurate data collection, forecasting inaccuracies, lack of integration with other systems, and resistance to change.
- Q: What are the benefits of using CRP software? A: Software enhances the accuracy and efficiency of CRP, providing real-time visibility into capacity utilization, and facilitating what-if analysis.
- Q: How does CRP impact lead times? A: By optimizing resource allocation and identifying bottlenecks, CRP helps reduce lead times and improve on-time delivery.
- Q: How can I improve the accuracy of my CRP process? A: This involves improving data accuracy, using sophisticated forecasting techniques, regularly reviewing and updating the plan, and involving relevant stakeholders in the process.
Summary
Addressing these questions highlights the critical aspects of effective CRP implementation and its contribution to overall manufacturing efficiency.
Tips for Effective CRP
Introduction
These tips can enhance the effectiveness of your Capacity Requirements Planning process.
Tips:
- Invest in reliable forecasting techniques: Use sophisticated forecasting methods to improve the accuracy of demand predictions.
- Maintain accurate data: Ensure data accuracy for bills of materials (BOM), routings, and resource availability.
- Integrate CRP with other planning systems: Link CRP with MRP and other relevant systems for a holistic view of the production process.
- Utilize CRP software: Leverage software to enhance accuracy, efficiency, and real-time monitoring capabilities.
- Regularly review and update the plan: Monitor actual production against the planned schedule and make adjustments as needed.
- Involve relevant stakeholders: Engage production personnel, management, and other relevant parties in the planning process.
- Prioritize bottleneck mitigation: Focus on addressing capacity constraints to optimize production efficiency.
- Develop contingency plans: Establish alternative plans to address unforeseen circumstances such as equipment failures or material shortages.
Summary
Following these tips will greatly improve your CRP implementation, resulting in increased production efficiency, better resource allocation, and reduced lead times.
Summary of Capacity Requirements Planning
This exploration of Capacity Requirements Planning (CRP) highlights its critical role in optimizing manufacturing operations. Effective CRP ensures that production plans are feasible, resources are utilized efficiently, and production deadlines are consistently met. By implementing a robust CRP process, businesses can significantly improve their operational efficiency, enhance on-time delivery performance, and gain a competitive edge in the market.
Closing Message
Capacity Requirements Planning is not merely a planning technique; it’s a cornerstone of operational excellence in manufacturing. By mastering CRP and integrating it effectively within the broader production planning framework, organizations can unlock significant improvements in efficiency, profitability, and competitive advantage. Continuous improvement and adaptation are essential for maintaining the effectiveness of your CRP system as your business evolves.
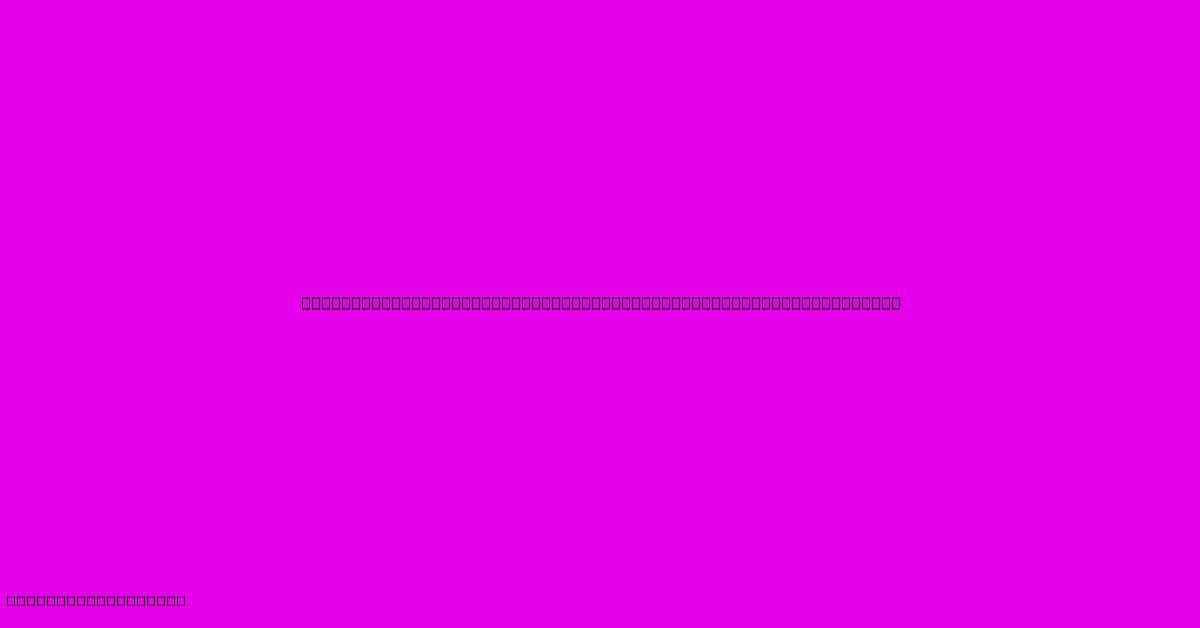
Thank you for taking the time to explore our website Capacity Requirements Planning Crp Definition And Procedures. We hope you find the information useful. Feel free to contact us for any questions, and don’t forget to bookmark us for future visits!
We truly appreciate your visit to explore more about Capacity Requirements Planning Crp Definition And Procedures. Let us know if you need further assistance. Be sure to bookmark this site and visit us again soon!
Featured Posts
-
How To Download Chase Credit Card Statements Into Excel
Jan 03, 2025
-
Nine Bond Rule Definition
Jan 03, 2025
-
How To Take A Life Insurance Policy Out On Someone
Jan 03, 2025
-
What Is A Dp3 Insurance Policy
Jan 03, 2025
-
Chaplain Malpractice Insurance Definition
Jan 03, 2025